London
Trailblazing fashion’s textile landscape since introducing the authentic crinkle.
2024 celebrates the 40th anniversary of Maxxam, a ground-breaking 4-way stretch and crinkle fabric that has captivated the fashion industry since its inception. Originating from the innovatively creative mind of Rosemary Moore in the early 1980s, Maxxam remains an extraordinary creation, distinguished by its unparalleled tactile qualities, universal one-size-fits-all appeal and well ahead of its time sustainable credentials, according to the London based brand. Today, the fabric continues to redefine the boundaries of comfort and style, it says.
Rosemary Moore earned her Master’s degree in Textile Design from the Royal College of Art in 1983. Drawing on her substantial expertise across all areas of fabric design covering commissioned, experimental, research, and forecasting, she unveiled the ground-breaking Maxxam fabric in 1983.
Making waves
The revolutionary creation made waves, captivating the imaginations of swimwear and fashion designers on a global scale, and quickly establishing itself as an influential force within the fashion industry.
Reflecting on the 40-year journey of Maxxam, Rosemary Moore expressed her excitement: “I am thrilled to be celebrating 40 years of Maxxam authentic crinkle. It was such a unique fabric when it launched, with the potential to fit a size 8 up to size 16-18. It became an overnight success, worn by everyone from Julia Roberts in Pretty Woman to the girl next door. Designers and brands eagerly embraced it, with renowned figures like Missoni, Katharine Hamnett, Australian designer, Brian Rochford, Janice Wainwright, and Speedo incorporating it into their collections.”
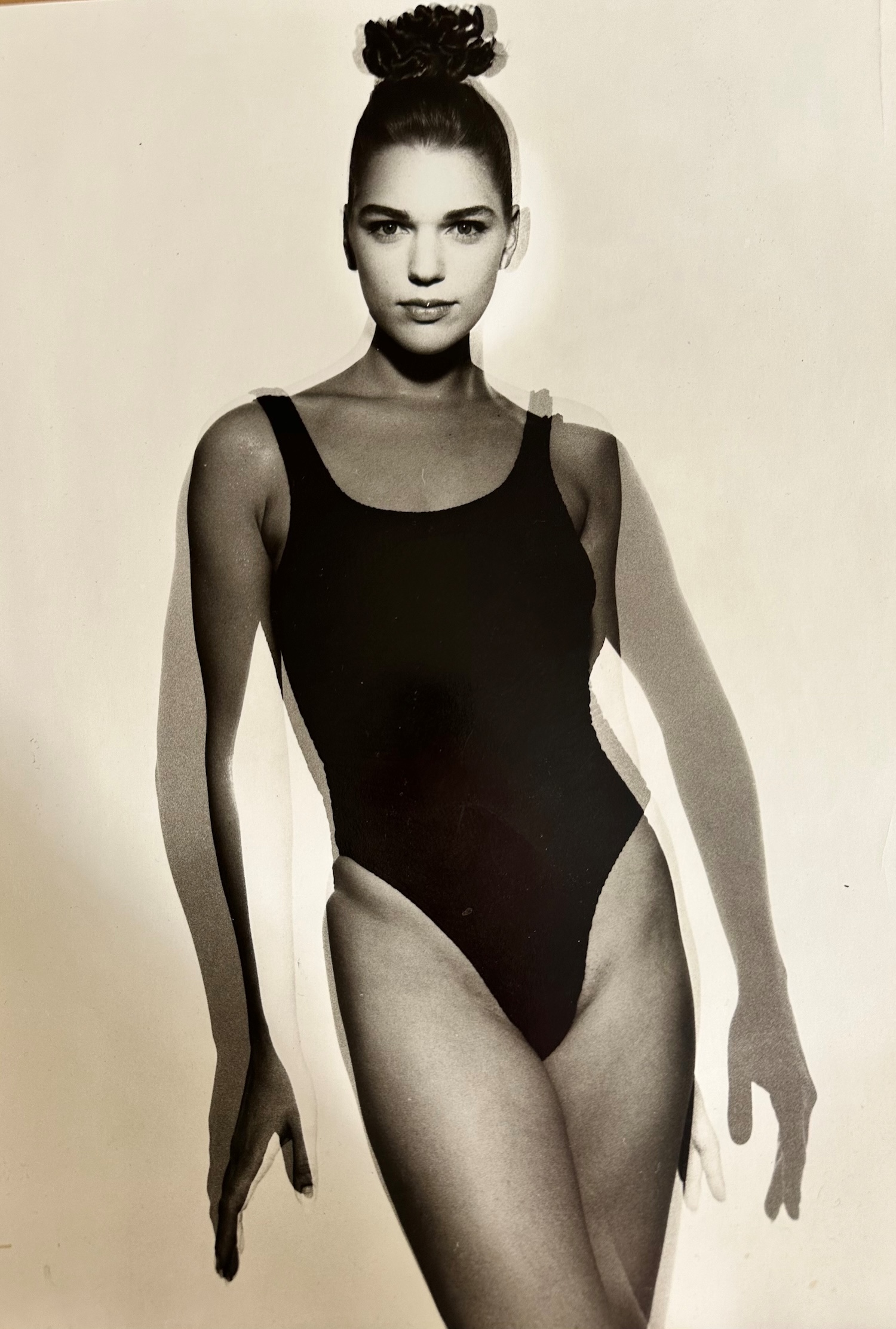
“When I developed Maxxam I did not realise at the time how advanced the idea was – even more relevant now with the cost savings it offers in low waste and low-cost manufacturing, with one size fitting all and the introduction of recycled fibres. The fabric was licensed worldwide and at the time we made it in the USA, Australia, and the UK under licence.”
A new home
In the early 1980s, once Maxxam was in production, it found a new home with London-based designer Liza Bruce, a connection Rosemary Moore made through her Royal College of Art show, and who propelled its success through innovative designs and original qualities. Targeting the luxury market, the swimwear gained international acclaim, with prestigious retailers such as Harrods, HN Browns, Selfridges and Liza Bruce’s own stores in Pimlico showcasing Maxxam’s unique allure.
The success of the fabric continued with the introduction of enhancements such as a double-knit jersey jacquard and a cord produced by Chatsworth Knitting. Additionally, esteemed licensees, including Heathcoats in Australia and Fabritex in the USA, played a key role in extending the fabric’s global reach. Soon Maxxam was seen on the likes of Tina Turner, Kelly LeBrock, Cindy Crawford, Bridget Bardot, Wendy James, and Whitney Houston.
In the late 1980s, Rosemary received a request to create items under the ‘Lycra Power’ theme, involving the creation of fabrics with diverse Lycra tensions and differing levels of compression. Drawing on her experiences as a gymnast, Rosemary understood that the tension of Lycra on the body had a proprioceptive effect on the mind and muscles to improve mental and physical benefits.
Japan
In 1987, Rosemary went on to unveil her own collection of womenswear, swimwear and coverups, featuring Maxxam jacquard fabrics. The body-conscious separates went beyond conventional boundaries, embracing a fusion of swimwear, streetwear, dance, and sportswear. Due to interest from Nihon Vogue, Rosemary put on a touring exhibition of knitwear in Japan called Masquerade.
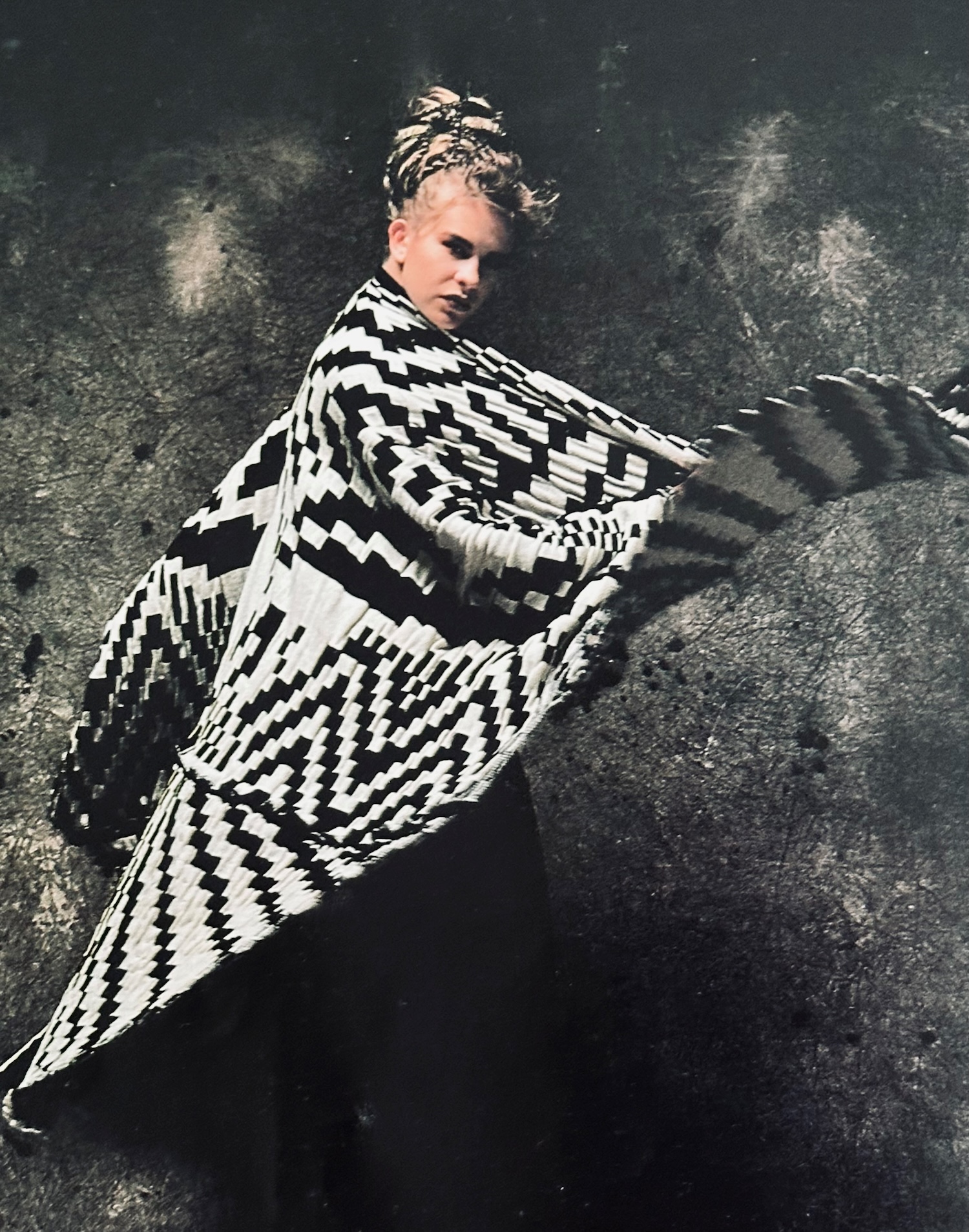
The collection went on to win the prestigious Fashion Foundation Award, judged by Issey Miyake and Comme des Garçons. Today, these garments are proudly displayed at the Victoria and Albert Museum in London featuring, a testament to the lasting impact of Rosemary’s ingenuity.
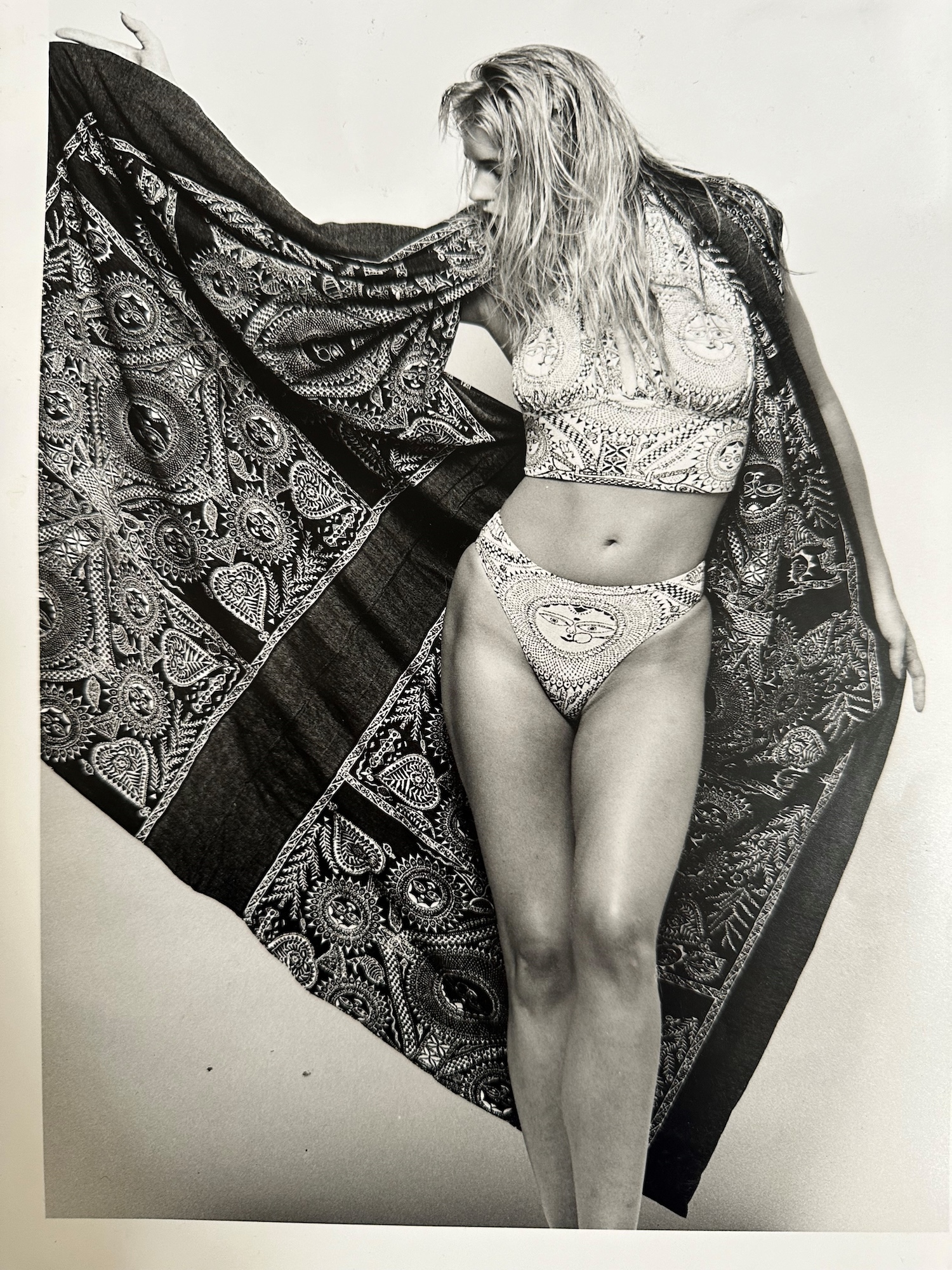
Following her success in Japan, Rosemary was approached by Nitto Boseki Co Ltd to license ranges of her textiles and clothing which led her to move to Japan and work with innovative equipment and yarns. She developed the ‘I Spy’ range alongside Rosemary Moore RTW which was launched at Tokyo Fashion Week, and successfully retailed in the UK with Dickins & Jones and Liberty of London.
In the 1990s, Rosemary’s collaboration with textile manufacturing bases in the UK included partnerships with Du Pont’s research and development centre unit in Gloucester. She worked with Ace Style Inc, the suppliers of Calvin Klein Intimates which were developed on Santoni machines at a time when they were being introduced to the market. Here she could work with their new and innovative yarns and try them out with British manufacturers. During this time, Rosemary also invented the first seamless trainer prototype with Dunlop using new technology discovered while on her placement as a student at Courtaulds and which all top trainer brands use today.
By the 1990’s Maxxam had shifted from being used in bodycon designs to swimwear. In 1995, Rosemary introduced the Stowaway fold-up collection which included swimwear, day and evening wear with each piece meticulously designed to effectively fold up into its own integral pocket, making it ideal for packing and travelling. It was soon stocked in House of Fraser, Fenwick, and Selfridges.
After moving on from collaborations with Hunza G, Maxxam crinkle fabric now has a successful creative partnership with Australian swimwear brand, Bond-Eye spanning 10 years, and online-exclusive label, Youswim. Steve Philpott, the creative force behind Bond Eye, meticulously shapes entire collections using the distinctive MAXXAM® crinkle stretch fabric.
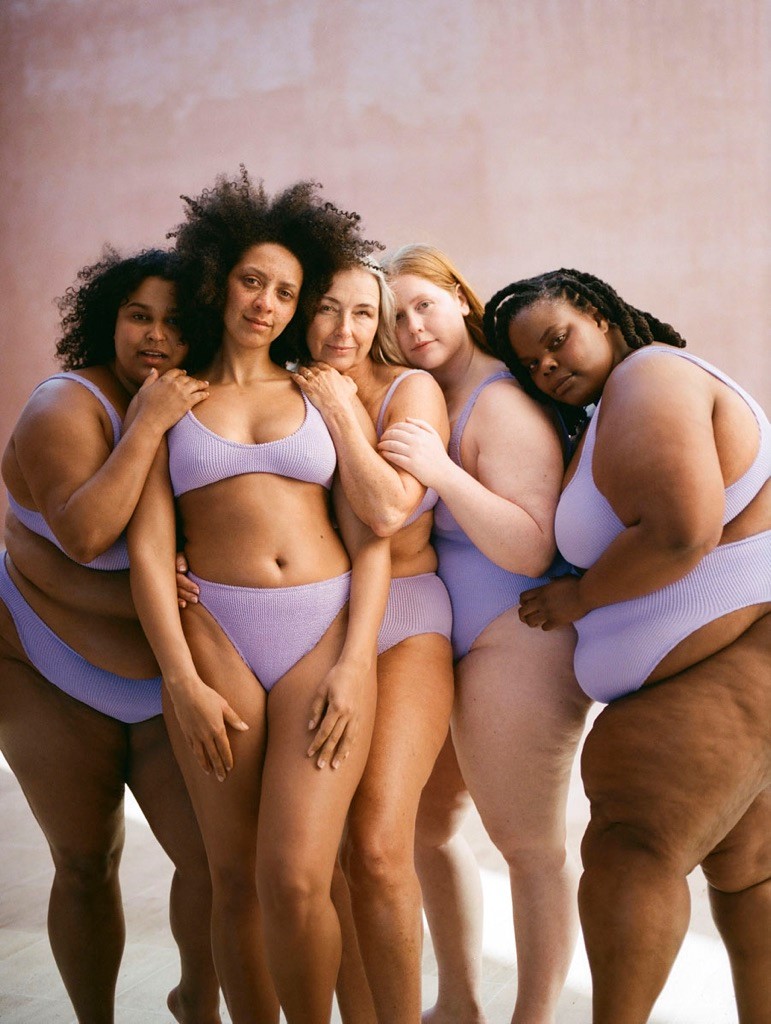
This innovative choice delivers one-sized swimwear that has resonated with women globally, including the likes of Lady Gaga, Kim Kardashians, Rita Ora, Daisy Lowe, Bella Hadid, Rihanna, and Miley Cyrus.
Although swimwear is the most popular end use today, the sheer versatility of the fabric means there are infinite uses.
Rosemary comments on the characteristics of the fabric as it is today: “Maxxam places a strong emphasis on surface effects, with its true attributes embodying a sustainable profile, pioneering concepts ahead of its time, with cost-effective manufacturing, minimal waste in off cuts, convenient one-size stocking in stores or online, and extended cloth longevity achieved through the use of recycled nylon GRS and Lycra Branded. Locally made in the UK, Maxxam ensures a positive proprioceptive effect on the body, as the Lycra tension influence both the mind and mental condition. Furthermore, the dyeing process is conducted nearby, contributing to reduced emissions.”
“We manufacture our products on high-gauge machines, while copies are produced on lower-gauge machines using polyester or inexpensive nylon. Employing the same yarn count as we did in the 80s with Tactel Type, our Lycra is of a unique and exceptional quality, exclusively crafted for us to ensure long-term recovery. Remarkably, people still wear Maxxam from the 80s, and we’ve even been contacted by people wearing suits handed down from their mothers during that era, attesting to the enduring quality and longevity of our products.”
Sustainable future
Rosemary is now exploring fibres derived from nature, particularly biodynamic fibres, as she works towards a more sustainable future, focusing on end-of-life biodegradability to move away from reliance on fossil fuels. An exciting new development being introduced in 2025 includes the new elastane yarn, with 80% derived from corn-based sources, presenting a potential direction for Maxxam’s next steps in advancing eco-friendly materials.
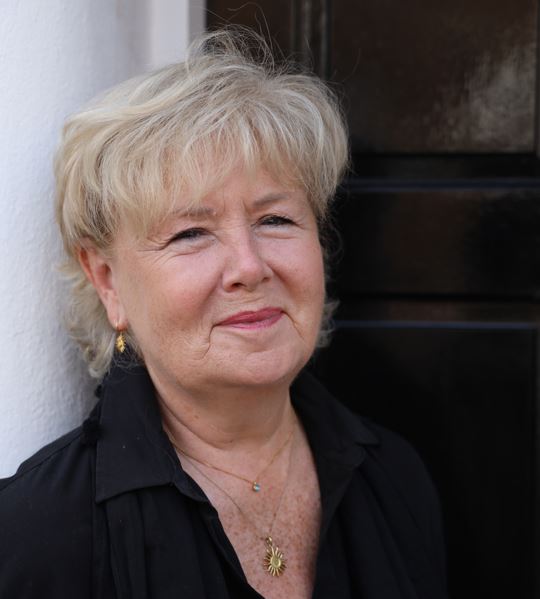
Rosemary comments: “We are currently engaged in the development of innovative textures, utilising our original technology on finer gauge machines to diversify our textiles. This expansion of our original intellectual property aims to encompass various apparel segments, including intimate apparel, sportswear, bodywear, swimwear, and separates. We will be launching these new offerings in Spring 2025.”
“In recent years, we’ve made adjustments to our original cloth structure, introducing fabrics that can accommodate a significantly broader range of sizes. This development brings us even closer to the realisation of a more inclusive one size fits all concept.”
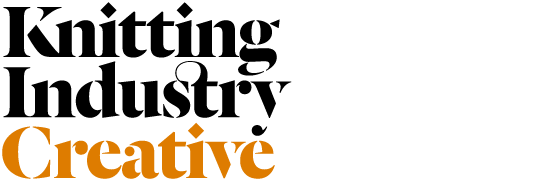
Subscribe To Our Newsletter
Join our mailing list to receive the latest news and updates from our team.