Premiere Vision took place last week in Paris in its usual location of Parc Des Expositions. We travelled to the French Capital to gain an insight on new developments in the textile industry and to attend the TexSelect (formerly Texprint) award ceremony.
At a glance, there has been a slight increase in the number of exhibitors this season, with a 2.6% growth in the offer versus September 2017 (2015 companies in total exhibited at the latest edition, compared to 1954 from last September). The increase was registered mainly in the fabrics, leather and manufacturing sections. The offer in the yarns section is still quite limited with a total number of 63 exhibitors, the smallest in the whole fair.
After a speedy registration, we headed towards Knitwear Solutions, the area dedicated to knitwear manufacturing where a broad selection of flatbed knitting companies showcase their products. The offer in this section has grown considerably since its first edition in 2012: there are now over thirty companies from the EU and the Far East exhibiting (mainly Eastern Europe and China) and a leading knitting machine manufacturer, Shima Seiki. In occasion of Premiere Vision, the Japanese company introduced a new addition to their range, the SVR093SP, a fully fashioning machine with inlay capabilities that features the new i-Plating technology. I-Plating offers inverse plating capabilities, so that two colours can be knitted on the same course and shown on different sides of a jersey fabric for a print-like or intarsia effect.
Combined with the inlay capabilities of the machine, the possibilities for new knit structures and fabric hybrids is enormous. We examined one of the samples that were being knitted live at the show: it had a very fluid drape that is characteristic of single bed fabrics, but with a very detailed graphic artwork reminiscent of a complicated intarsia-we were told that images could be programmed down to each individual stitch for a very clean and realistic effect. Because of the nature of plated fabrics, the machine works with two feeders only, alternating various areas of colour in the same course and eliminating the programming complications and elevated costs of intarsia fabrics. Coupled with the new R2CARRIAGE System, the machine is able to produce plated fabrics at very rapid speeds. Shima Seiki also presented a new collection of garments which features their latest technical advancements in Wholegarment technology: embellishments very similar to embroidery stitches or appliqué can now be knitted integrally as part of the garment.
The selection of knitwear manufacturers was quite diverse: along some traditional mills we found some other companies that were more devoted to experimentation and research. Ben Juniper (www.benjuniper.com), a leading manufacturer from Taiwan, presented a collection of colourful samples with a unique artisanal look: particular attention was given to yarn selection, texture, stitch patterns and heavy gauges for a true hand knit feel.
In a multitude of fine gauge, ordinary sweaters in muted colours, their collection really stood out. Flora Chen, from the design team, explained that craft is at the heart of the company. Old, outdated techniques are revisited and developed with the latest technologies from both Shima Seiki and Stoll. Although Ben Juniper have over three hundred machines, hand crafted techniques like hand knitting, embroidery and crochet are still integral to the company’s ethos. Offering a complete solution from colour matching, yarn spinning, manufacturing and delivery, Ben Juniper work with the likes of Zara and Anthropologie but can also cater for much smaller companies.
This lively enthusiasm for experimentation and development was not reflected in the knitwear solution forum unfortunately: the fabrics on display lacked a sense of cohesion, of history. There didn’t seem to be a clear direction for a season, the colour story was very similar across the various themes and some of the fabrics felt a bit too heavy and cumbersome for the fashion market. At the centre of the forum there were some garments on display produced by the manufacturers that exhibited in this section, but even these pieces failed to captivate any real interest, or suggest a strong sense of trend direction: the combination of yarns and stitch structures were very ordinary and the silhouettes were basic. On the other hand, there was a number of companies in the Yarns section that pioneered some very innovative, sustainable processes and that could have been included in the forum. Their innovations could have been explored further with the expertise of the manufacturers and knitwear designers at the show, it would have been interesting to see some more refined proposals on how these new advancements can be utilised in the fashion industry.
“Perma Corporation” (www.permacorporation.com) was one of these exhibitors that caught our attention: the Thai company has developed a permanent anti-bacterial textile using an exclusive nano-Zinc technology that prevents the growth of harmful bacteria. Antimicrobial textiles are conventionally used in medical environments, but with the exponential growth of global travel and with the development of new, faster means of transport it is very clear to see how infectious diseases can spread at an increasingly rapid rate today. From a designer’s point of view, the evolution of such textiles is an exciting development that will also have a dramatic impact on the direction of fashion and how garments are conceived. It is becoming almost anachronistic to design collections based solely on aesthetic qualities or a creative director’s idea of beauty: designers should make a greater effort to use effectively these new advancements to challenge the stagnant climate that fashion finds itself in. It would be fascinating to see how these innovative fabrics could evolve into desirable fashion items that are aesthetically appealing, functional and environmentally clean.
Design innovation is also one of the core elements of Premiere Vision: Hall 5 is the usual home of Premiere Vision Design, a creative hub where many print, knit, weave and embroidery studios showcase their work to the industry. Texselect (formerly Texprint), the British organisation that champions the work of the best Textiles graduates in the UK also exhibited in their village in Hall 5. Every year TexSelect award several prestigious prizes to their candidates during Premiere Vision. Matthew Briggs, a recent Knitted Textiles graduate from the Royal College of Art, was this year’s winner of three prizes: the Fashion prize, sponsored by Texselect, the WGSN Textiles of The Future Award and the Woolmark Company TexSelect Award. Matthew’s work is a colourful, tongue-in-cheek representation of some fictional rivalry between gangs of pearly kings and queens. Using mainly Cashwool, he mixes the aesthetic of vintage wrestling posters with American football, creating vibrant fabrics in various gauges. Matthew has done a great deal of experimentation with Shima’s inlay machines, mixing this technique with tubular knitting and monofilament. His fabrics are very graphic, almost print-like, with a confident, strong handle and some inviting tactile qualities. Matthew’s technical competence and yarn expertise is evident in some of the pieces that he designed on hand flat machines: sturdy, plush fabrics are reminiscent of vintage sports towels, big volumes in his garments are achieved through clever linking methods that allowed him to mix knits in various gauges.
Photo credit: Carlo Volpi
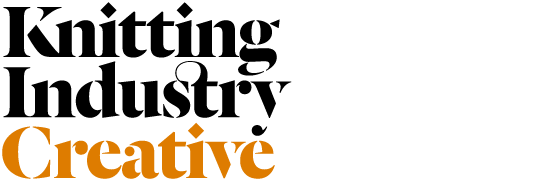
Subscribe To Our Newsletter
Join our mailing list to receive the latest news and updates from our team.