Delft, The Netherlands
Unusual building structures can be created more efficiently and more sustainably using 3D knitted textiles.
The bearing structure of a building made out of knitted material. Mariana Popescu, Assistant Professor of Parametric Structural Design and Digital Fabrication shows that unusual building structures can be created more efficiently and more sustainably using 3D knitted textiles. She hopes her innovative approach will inspire new generations of designers and engineers to think outside the box.
Knitting is only a small part of my research, I’m much more of a designer and programmer
For those who think knitting is for old ladies in rocking chairs: you’re way behind. Computational architect and structural designer Mariana Popescu is not into knitting woolly beanies or winter scarves and cardigans. Her knitting machine is producing building constructions instead, which, Popescu says, can play an important role in the construction of complex building geometries. “These can be, for example, arches or domes that span a big space, such as a bridge or the roof of a museum or sports stadium.”
Sustainability and complex geometries
Although straight flat shapes are cheaper and easier to build, doubly curved geometries are also used in buildings and not just because they look pretty, Popescu says. “Curvature also adds strength. Think of paper. If you hold upa sheet of paper ad press down on it, it cannot sustain the load and it bends. But if you fold it into a harmonica shape, it is a lot more resilient. And you’re using the same amount of material. It’s the same in buildings.”
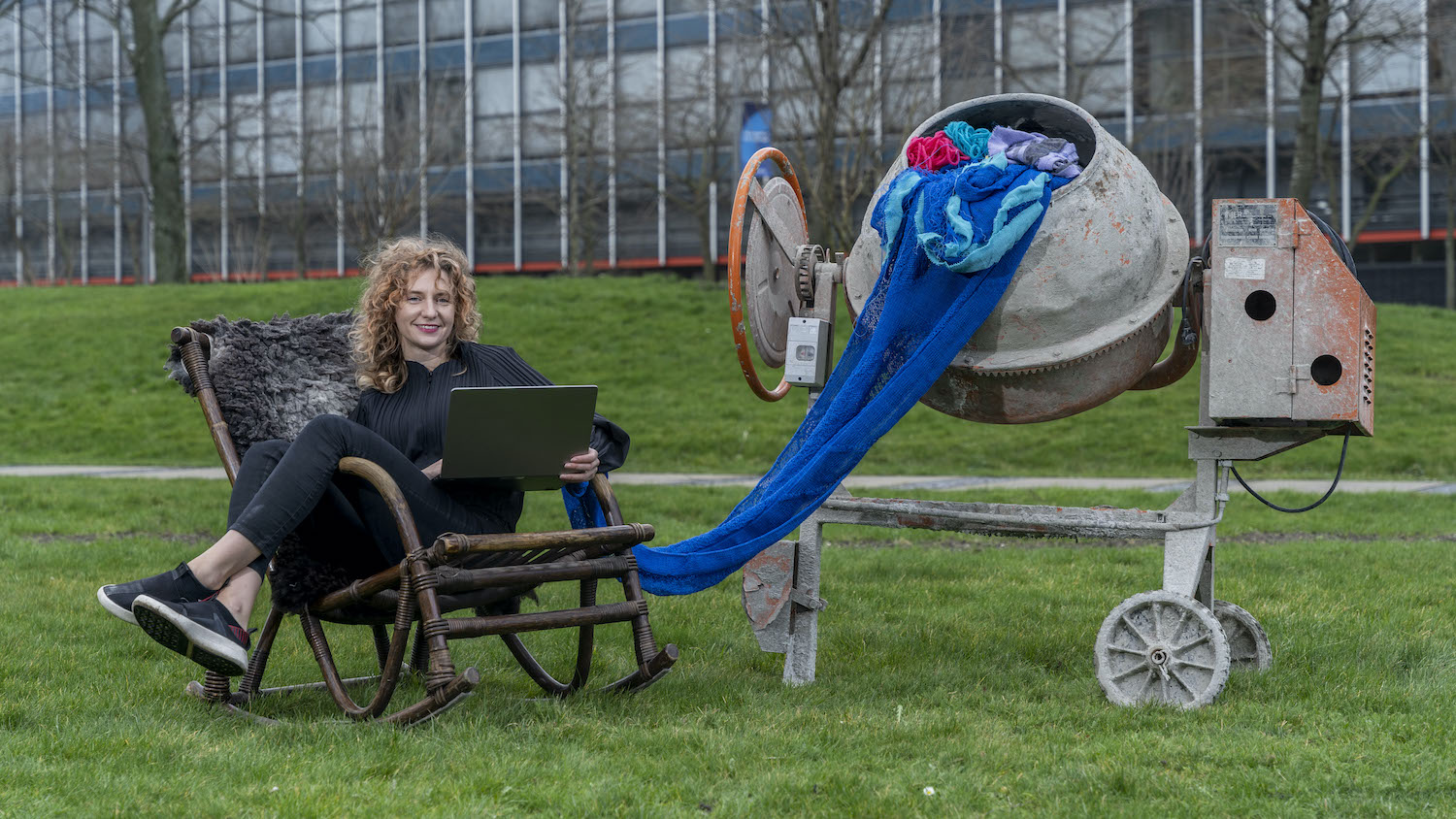
To create doubly curved shapes, traditional methods often use timber or milled foam moulds, a process that is very labour intensive and not sustainable, considering these moulds are often single-use, Popescu says. “You need an incredible amount of material to make a complex formwork and very often that material cannot be reused. That is why I’m looking at ways and materials to create complex geometries as efficiently and sustainably as possible.”
Efficient materials and design
When Popescu was a team-member of the TU Delft’s Nuna solar car, she gained a number of valuable insights. “The construction of a car is of course completely different from that of a building but they do have a couple of things in common. Efficient use of material, design and weight, for example. For the Nuna we used carbon fiber. Carbon fiber textiles are not commonly used in architecture or construction but to me the lightness of using textiles made them all the more interesting.”
During her PhD research at ETH Zürich, Popescu explored the application of textile as a flexible formwork system. She also decided to use a knitting machine. “You can feed different materials into a knitting machine. We will have to see if all these smart yarns can be applied in building.”
Big 3D surfaces
The use of textile in building constructions is not completely new, Popescu says. “It has been tried before throughout the 20th century but it didn’t really get off the ground. Generally the textiles used for such flexible moulds come in rolls of flat material. If you want to make a doubly curved geometry, you have to cut the textiles and sow the pieces much like you do with tailoring.” Thanks to 3D knitting it is possible to produce these geometries in just one piece, including features such as channels, openings and groves. To do so, a knitting machine needs precise instructions. It requires expert knowledge to relate the machine operations to the resulting geometry or feature. For big surfaces with a complex shape, only the most skilled technicians can design these machine instructions.
Algorithm to the rescue
Popescu remedied the problem by creating an algorithm for the knitting machine which gives it instructions. “The machine then generates 3D shapes during the knitting process. The algorithm tells it when a needle has to come into action, for instance, and when not. The instructions have been put into a pixel grid. The different colours of the grid represent different needle actions. The algorithm first turns the building design into a pixel grid, translating it from 3D to 2D. The machine then gets to work on the final 3D product in textile.”
I’m constantly pushing the limits of the machines I use
The ‘knitting lady’
Popescu’s colleagues are calling her the ‘knitting lady’, a nickname she feels she doesn’t really deserve. “First of all, I can’t knit! The machine is doing it all for me. But most importantly, knitting is only a very small part of my research. I’m more of a designer and programmer. I like to use technology to realise my designs in as smart a way as possible. That means I’m constantly pushing the limits of the machines I use. The building of the construction itself I regard as the cherry on the cake.”
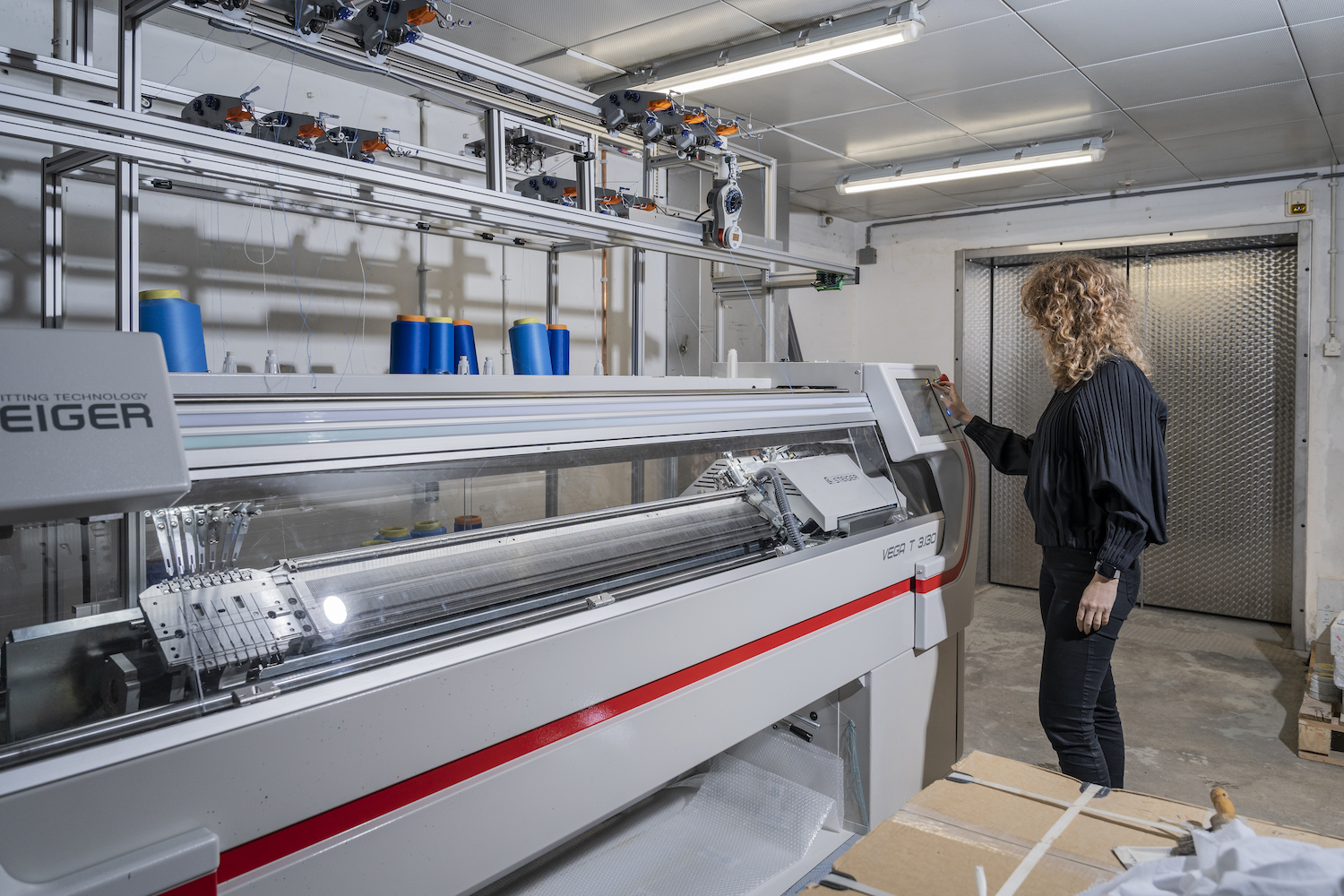
Interdisciplinary cooperation
Popescu hopes that the links in the building chain will fit together more snugly in practice as well. “At the moment the whole process is often very fragmented. First the architect makes a design and sends it to an engineer who does the calculations and thinks about how to put it all together. Then the builders get to work. But then, later on in the process, it turns out that something is very difficult to do, or that it produces a lot of waste. If all parties were to think about structure, technology, material, and fabrication from the get-go you would end up with a design that is much more feasible and sustainable.”
A building knitting bug?
Sustainable building using knitted textile for constructions could be useful, Popescu says, but it is not a one size fits all solution. “We need to look at each situation individually to determine how we build and which materials we use. We need to ask what means are available locally and how practical a project really is. I hope that out of the box thinking and a constant search for innovative tools will help tackle societal challenges and inspire a new generation of architects and engineers.”
About Mariana Popescu
Mariana Popescu’s research into the use of more sustainable building materials earned her the title of ‘pioneer’ in the MIT Technology Review Innovator Under 35 in 2019. Last year a 9-metre-wide knitted construction was exhibited at MAXXI Museum in Rome, a joint project of the CEG department at TU Delft and The Block Research Group at ETH Zürich.
Article republished with the kind permission of TU Delft.
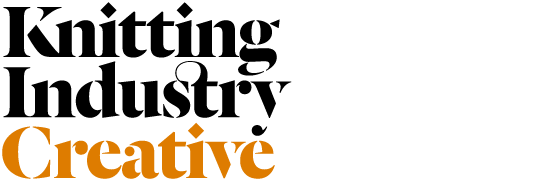
Subscribe To Our Newsletter
Join our mailing list to receive the latest news and updates from our team.