Article republished with the kind permission of UK Fashion & Textiles (UKFT)
Ian Maclean, Managing Director of John Smedley, discusses the effect of the coronavirus pandemic on his business and how, when the time is right, the company is determined to provide an environment that is safe to work in, but also one that makes people feel safe.
We ran a two-stage temporary shutdown of our business in March. In response to the Government lockdown order, we closed our three shops in London on the 20th March, and then we took the decision to shut down our two factories on the 27th March. Luckily, we had a few days to plan for the factory shutdowns, which allowed us to do things like clean and oil the machines, cover them, and protect our Work In Progress by putting it into proper storage bags.
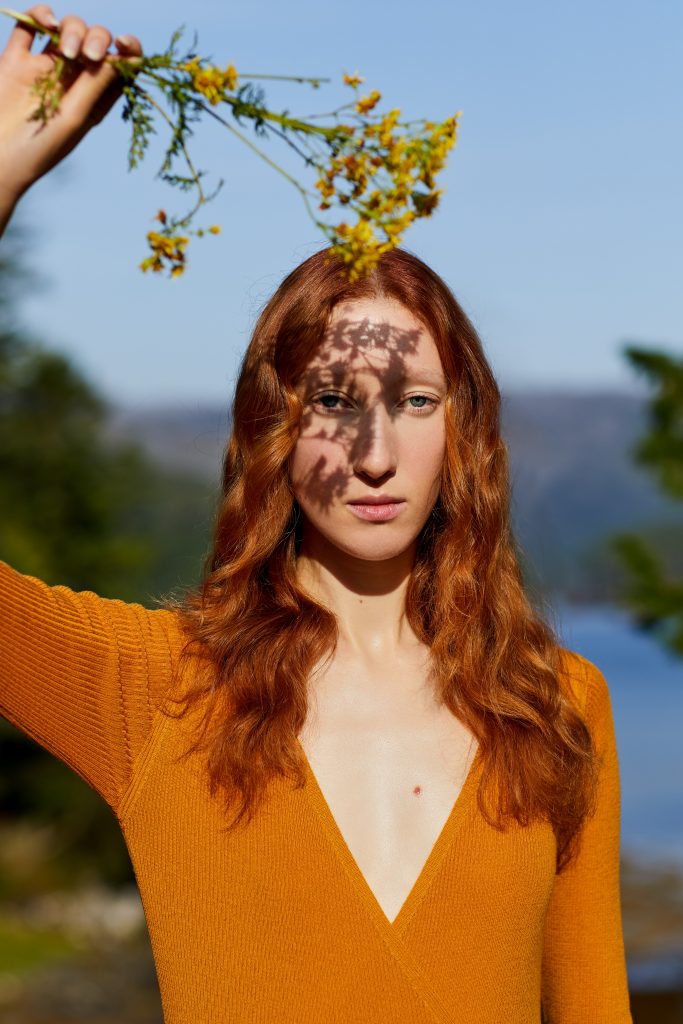
It did feel as though the right point had arrived for us to go into shutdown. In the middle of March we had begun to experience employees directly involved in manufacturing not working for various reasons: some were self-isolating themselves, others were doing so because someone in their families were showing symptoms, and some were living with elderly parents or had caring responsibilities. Rightly, most people wanted to be at home. Around the same time, our Italian supply chain for raw materials came to a complete standstill and this led to insurmountable bottlenecks in the process.
The speed at which everything happened left us reeling to a degree. Advice from Government was changing daily and was at times unclear and difficult to interpret. Demand dropped to near zero, and supply did as well once we were closed – a situation that is hard to grasp, even for my most experienced business colleagues. I spent a lot of time on the phone to my contacts in industry to try and get their take on what we were being told! The Chancellor’s plans for supporting industry were welcomed, but the degree of uncertainty we face has not lessened. We decided to go for a three week shutdown initially, which takes us to 17th April (we will review this in the light of Government advice later this week), but it is very unlikely we will be able to re-open any time soon. We furloughed around 320 of our 365-strong workforce, covering manufacturing, retail and most managers. We committed to paying 80% of pay and topping this up above the Government’s Coronavirus Job Retention Scheme’s £2,500 limit. The Directors accepted a 20% pay cut. Most of those who are retained are working from home and following all the necessary Public Health England guidelines.
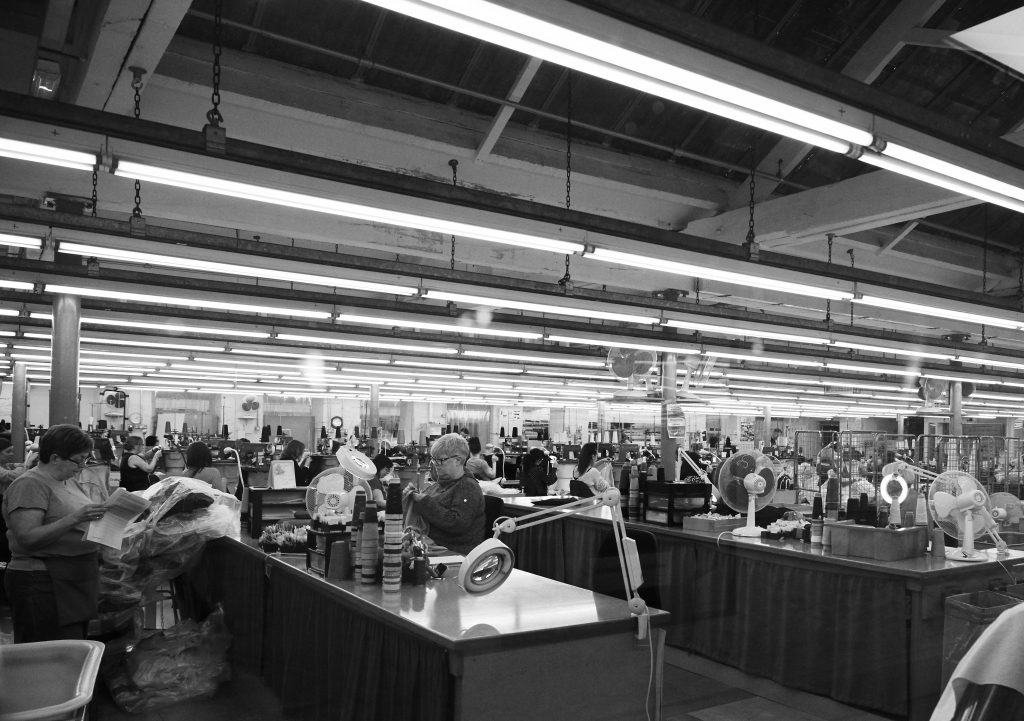
Our online business (www.johnsmedley.com ) is still open and trading – it is our only source of income right now. Our customer service team are processing the orders and responding to customer queries from home. A dedicated team of volunteers is working in the warehouse to ship goods out. I am also working in the warehouse every day with our team and we are following all correct health precautions.
My 80 year old parents are self-isolating at their home in Herefordshire, around 100 miles from here. We speak on the phone regularly, but I don’t know when we will see them again. I am acutely aware of the catastrophic affect the virus could have on their health, and I understand that the national conversation has to be around saving lives – right now it is health and not the economy that is of prime importance. This could go on for some time.
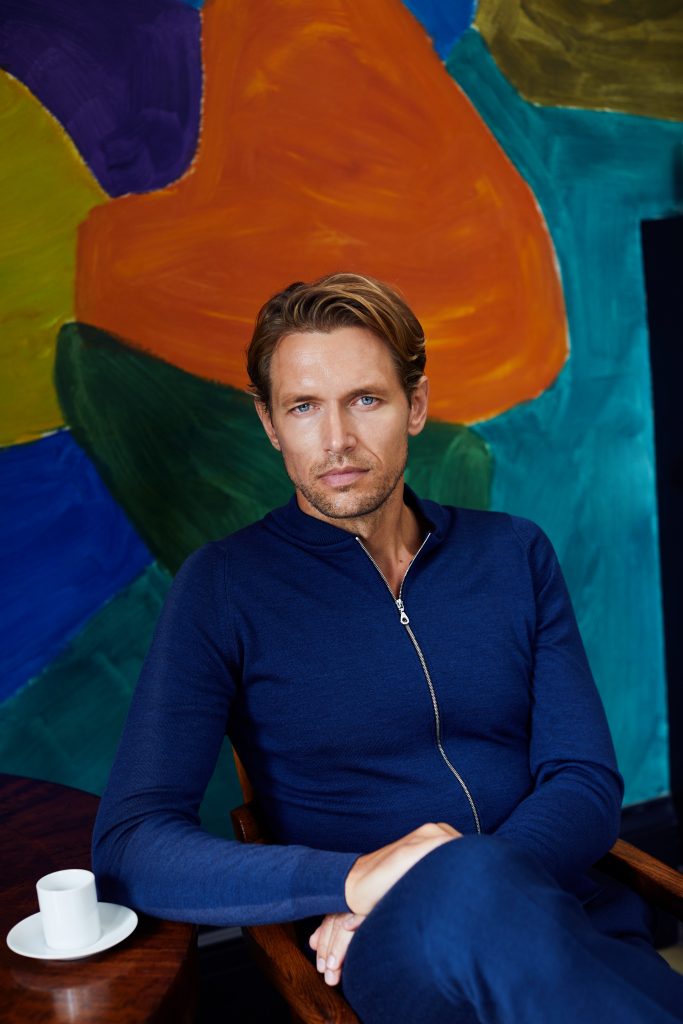
At some point, however, it is inevitable that we will have to go back to work. In order to do this right, we will have to be very safe by following the rules rigorously. But this will not be enough, we will need to win hearts and minds too – the national conversation will have to evolve to become health and the economy. This will require resolve from the Government, some very clear messaging, and a great deal of positivity from the rest of us.
Our top team are already thinking (we surely have the time to do it!) about a project we are calling “Work Safe”. Our Health & Safety officers are gathering best advice from Public Health England, the Health and Safety Executive, the Unions and other manufacturing companies who are thinking along the same lines.
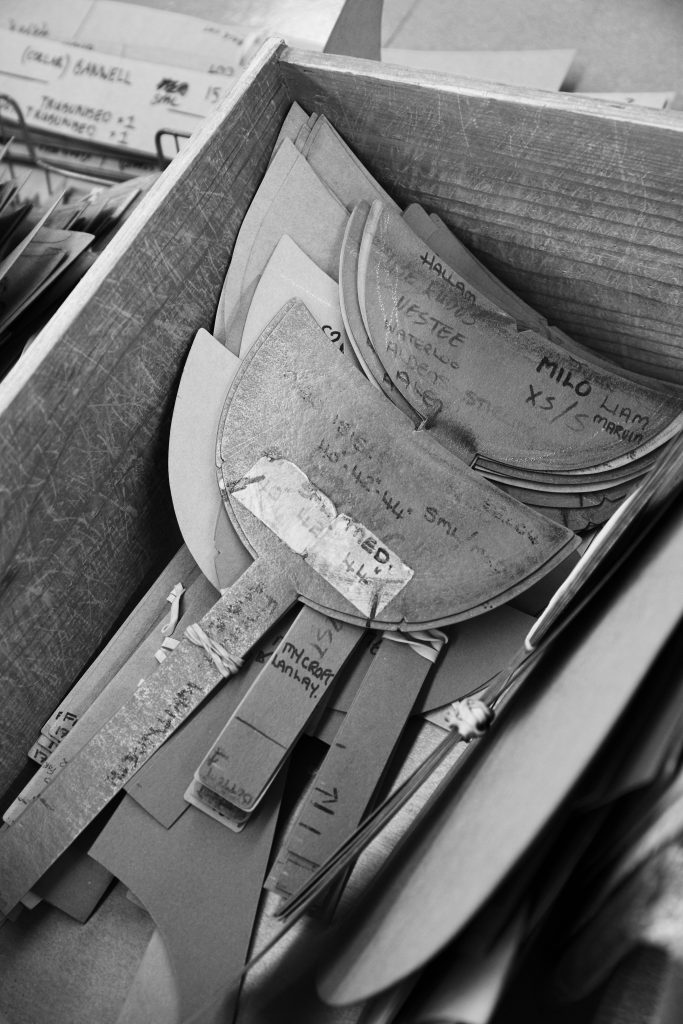
Anyone who visits a supermarket to shop will have seen how quickly these organisations have adapted their spaces to the new situation – and they are still learning. We are brainstorming ideas for re-arranging work processes in the factories to maximise distances between work stations, mapping one-way routes through the work rooms, designing barriers (like the Perspex ones you see appearing in the shops), planning enhanced cleaning rotas, and searching for the right PPE for staff to use. When the time is right, we are determined to provide an environment that is safe to work in, but also one that makes people feel safe.
It is very unlikely we will reopen the factory all at once, we will be more likely to bring people back in phases. I expect in the first phase, we will ask for volunteers and we can introduce people from there.
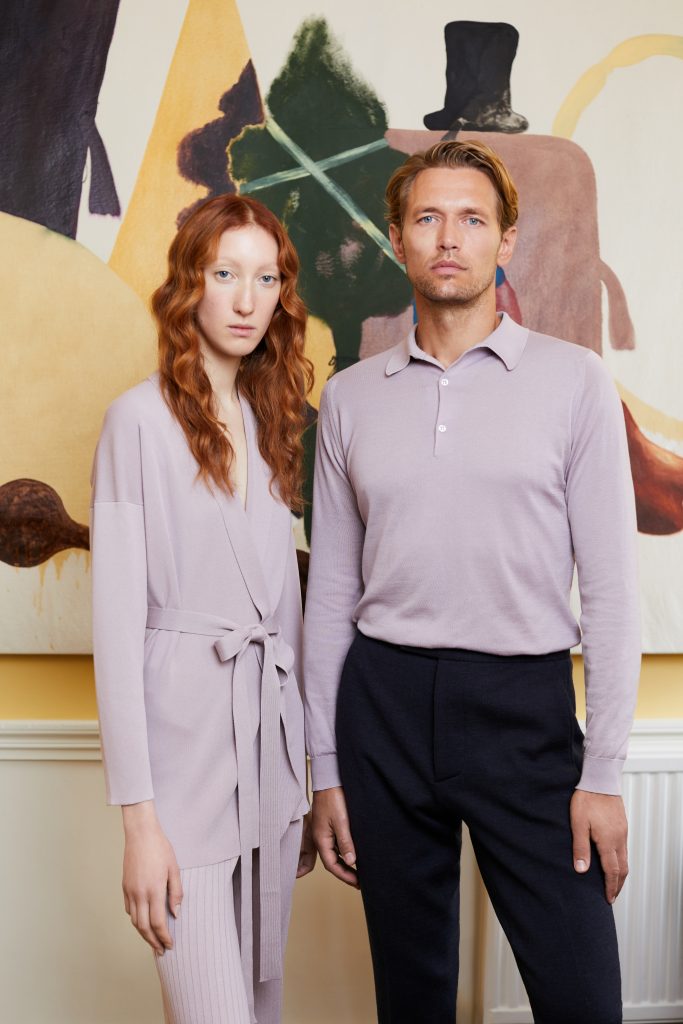
The second challenge we are facing is that we are predominantly a wholesale business. We took AW20 orders back in January that we are supposed to be manufacturing now for delivery in July. The longer that both retail and manufacturing are closed, the greater uncertainty there is around what products the retailers will eventually need to stock in their shops in the Autumn. This is a huge problem for the entire supply chain. We will need to somehow have conversations with customers to see what they really want going forward. We are thinking about approaching this problem in two stages. First, we’re going to be talking to our biggest customers and asking them to prioritise what they want as quickly as possible. This will give us a steer on what they are thinking. Second, I’m convinced that we will need to simplify some of our ranges, to help the smaller customers focus on getting delivery of our best sellers first. Our business is divided into seasonal “fashion” collections and repeating “classics”, and perhaps it will be that we have to drop some of the more fashion pieces as part of that conversation. The real question is when can we start the process of doing all of that – I don’t know.
My final thought is that the shutdown process is likely to turn out to have been much easier than starting up again. When we were in it, shutdown didn’t seem easy – it was a bit of a panic – but to be honest, opening up again looks like it could be ten times as hard. I think, for two reasons: supply chains are going to get worse before they get better, and customers are going to naturally be defensive of their cash. Whatever cash headroom any business has coming out of this, it will be stretched a lot further than before. My fear is that more businesses could go bust during the re-start phase.
This situation is changing so quickly that I’m sure we will be in a completely different place in a few weeks time. I pray it will be a better place!
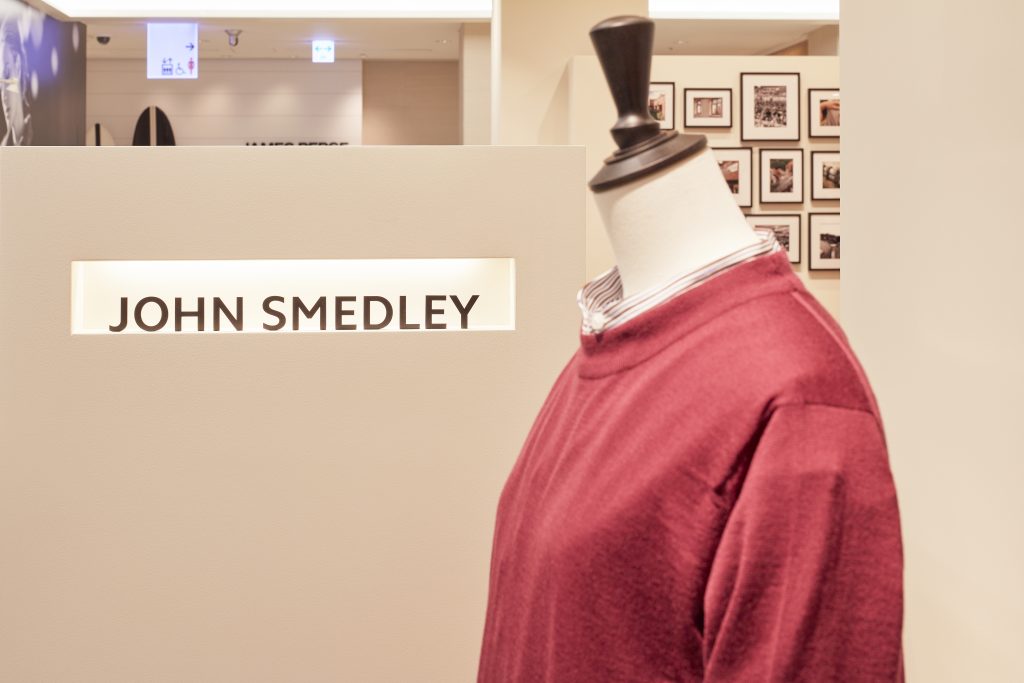
Article republished with the kind permission of UK Fashion & Textiles (UKFT)
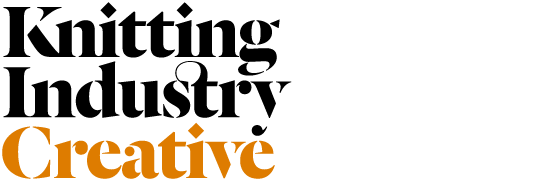
Subscribe To Our Newsletter
Join our mailing list to receive the latest news and updates from our team.