This London Design Fair, Research at RCA presents Design < > Research, the first instalment of a series of exhibitions for radical discussions on a more sustainable future between industry, designers, research centres and academics.
The work presented during the exhibition is an ongoing project by two newly established research centres at the College, the Intelligent Mobility Design Centre and the Burberry Material Future Research Group. The Industrial Strategy, the government’s plan to create better jobs for people and boost productivity, have pinpointed four Grand Challenges that as a society we need to approach to transform our future: artificial intelligence and data, an ageing society, clean growth and the future of mobility. Both centres are working to provide creative solutions to these challenges, and the first results of their investigations are presented at the show.
The Burberry Material Futures Research group’s aim is to develop new sustainable materials and processes that can be implemented across the industry. With access to design-led practitioners and with the expertise of engineering and material scientists, the research group will work across three main areas: sustainable future materials, sustainable future manufacturing and sustainable future customer experience.
The Intelligent Mobility Design Centre (IMDC) was established in 2016 to develop new approaches in the automotive industry within a fast changing global environment. The centre works with in house experts in collaboration with institutions like the government and the military on several live projects with the aim of creating innovative transportation methods to improve people’s quality of life.
The exhibition opened with a selection of new and experimental materials that can be utilised across several industries, most of these were initial ideas that still need a lot of refinement and research.
“Pulp-It” is a wearable paper based textile developed by Prof. Kay Politowicz and Dr Kate Goldsworthy from the Centre of Circular Design and Hjalmar Gransberg, Research Institute of Sweden (www.circulardesign.org.uk). This material was presented in the form of a t-shirt, with an intentional short life-span. Pulp-It acknowledges the impact of fast fashion in our society, but instead of changing people’s perception on the topic, it enables consumers to take part in this disposable culture without creating any damage to the environment.
“Chip[s]board®” (www.chipsboard.com) is a sustainable and biodegradable alternative to MDF created by Kingston graduates Rowan Minkley and Rob Nicoll. Whilst at college, the two designers became aware of the large amounts of MDF that the college was throwing away, often after a single use. This is a common practice unfortunately, so Minkley and Nicole set out to research a cleaner alternative. After a year of constant experimentation, they developed a material derived from potato waste. Unlike MDF, Chip[s]board® has no added toxic chemical or formaldehyde, making it 100% biodegradable. The company’s website is still under construction but this promising innovation has some potential developments even beyond chip board: the two designers are already working on some bespoke products that will go on sale on their site.
On display next to Chip[s]board® we found a soft, leathery material called Malai. This textile is currently made in India and was developed by two design graduates, Zuzana Gombosova and Susmith C.S. The pair met in India where Gombosova had travelled to research a traditional method for growing cellulose fibres, they both shared a common interest in crafts and sustainability which brought them together on the journey to discover and perfect Malai. This new fibre is made from waste coconut water, which is collected in big vats and sterilised. This process creates a nutrient environment where bacterial cultures can thrive. After a fermentation period of two weeks, the material is enriched with natural fibres and gums to improve its durability and is then dried.
Another item that featured an interesting textile was Speedo FastSkin Triathlon Suit (www.speedo.com). The woven fabric used for this item was inspired by shark skin: according to research, these animals can slip through water ten times faster than fish with smooth skin. The team at Speedo set out to investigate the reasons for this, and they realised that sharks are covered in small denticles of various sizes and lengths. These teeth-like structures are localised in certain areas of the body to facilitate faster gliding through the water. Following the same approach, the company has designed and made a swimming suit that seems to have very promising results: athletes who wear the fastSkin Suit have broken 18 out of 26 Olympic records.
Sharklet (www.sharklet.com) is a process that was also derived from the study of shark skin. Discovered by Dr Anthony Brennan, Sharklet uses the same dermal denticle idea to repel the formation of bacteria. During his initial studies, Dr Brennan realised that the topography of shark skin makes it impossible for any micro organism to cling on it. The purpose of his research was completely different (he was commissioned by the US army to find a better solution to stop algae from coating submarines), but the outcome had an incredible potential: if micro-organisms could not cling on shark skin, neither could bacteria. Sharklet is now producing some medical equipment, like wound dressings and endotracheal tubes, that mimic the surface of shark skin and that naturally repel bacteria.
Antimicrobial textiles were also the subject of investigation of travel wear start up Immunotex (https://www.lindsayannhanson.com), in collaboration with Margot Vaaderpass and Zaki Musa. The number of antibiotic resistant bacteria is increasing dramatically, as is global travel, so infections can spread a lot more easily across many continents. Travellers also expose themselves to more strains of bacteria and are more prone to infections. It is estimated that around 700,000 people die every year because of drug resistant bacteria, so it is vital that some alternatives to medication are researched. Immunotex designed the “Resistance runner” a shoe that is very lightweight and comfortable, ideal for people on the move. A culture of friendly bacteria, acting as a shield for the infectious organisms, is grown on the spongy material that composes the shoe. Immunotex plan to develop a whole collection of garments with the same type of technology in the near future.
Mindful manufacturing is a very important aspect for the future of the fashion industry, minimising the impact on the environment and developing sustainable methods of production is just as important as researching clean materials. Knitting is a perfect solutions to many of these problems: with the latest 3D knit and software developments we are able to produce garments without the need for sampling (which reduces delivery and material costs) and with zero waste. Zanni Maglieria (www.zannimauro.com) were amongst the first companies in Italy to use 3D knit for their manufacturing process. Ten years down the line, their level of expertise has grown considerably and so has the technology. 3D knitted fabrics have been developed to have outstanding structural properties, with very good resistance and thermal properties. The garment in the exhibition was a very fine, transparent polyester top with lace stitches that shows in detail the technical versatility of this technology.
This exhibition was the first instalment of a wider research project that will run for the next three years, The Royal College of Art extend an invitation to companies and organisations who might be willing to participate in collaborative projects.
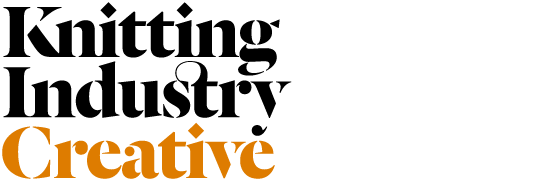
Subscribe To Our Newsletter
Join our mailing list to receive the latest news and updates from our team.