In celebration of their 60th anniversary, Shima Seiki shared a collection of online events. Keynote speeches by industry experts as well as videos showcasing Shima Seiki’s technological and software capabilities presented a snapshot of the innovation Shima has created over the past six decades.
Building relationships with institutions to further innovation in a variety of fields has been an important part of Shima Seiki’s growth. A keynote presentation from MIT Media Lab (Cambridge, Massachusetts) director Dr. Dava Newman detailed how their research utilises Shima Seiki technology, whilst sharing what the next decade holds for their partnership together. Amongst the collective research threads Dr Newman shared surrounding complex systems, human machine networks and transformative technologies, a particularly exciting knitted research development ‘Second Skin Design, BioSuitTM for Human 2.0’ was discussed.
Shima’s 3D knitting technologies are being utilised within this research process at MIT Media Lab by advancing the Media Lab’s knitted body suit performance. The project is exploring methods of achieving maximum flex and extension capabilities within the elbow area of the suit, with integrated pressure sensors. The aim is to create a ‘second skin’ knitted body suit, custom made to the wearer which can be utilised in interplanetary explorations. These cross-sector collaborations are an exciting part of Shima’s ever growing industrial network.

Software developments have been a defining part of Shima’s identity in their most recent decade. Their SDS ONE Knit Paint Software was shared within one of their videos, displaying efficiency improving functions. This was particularly useful for beginners as their ‘You have to know it’ video covered some of the lesser-known functions within their software.
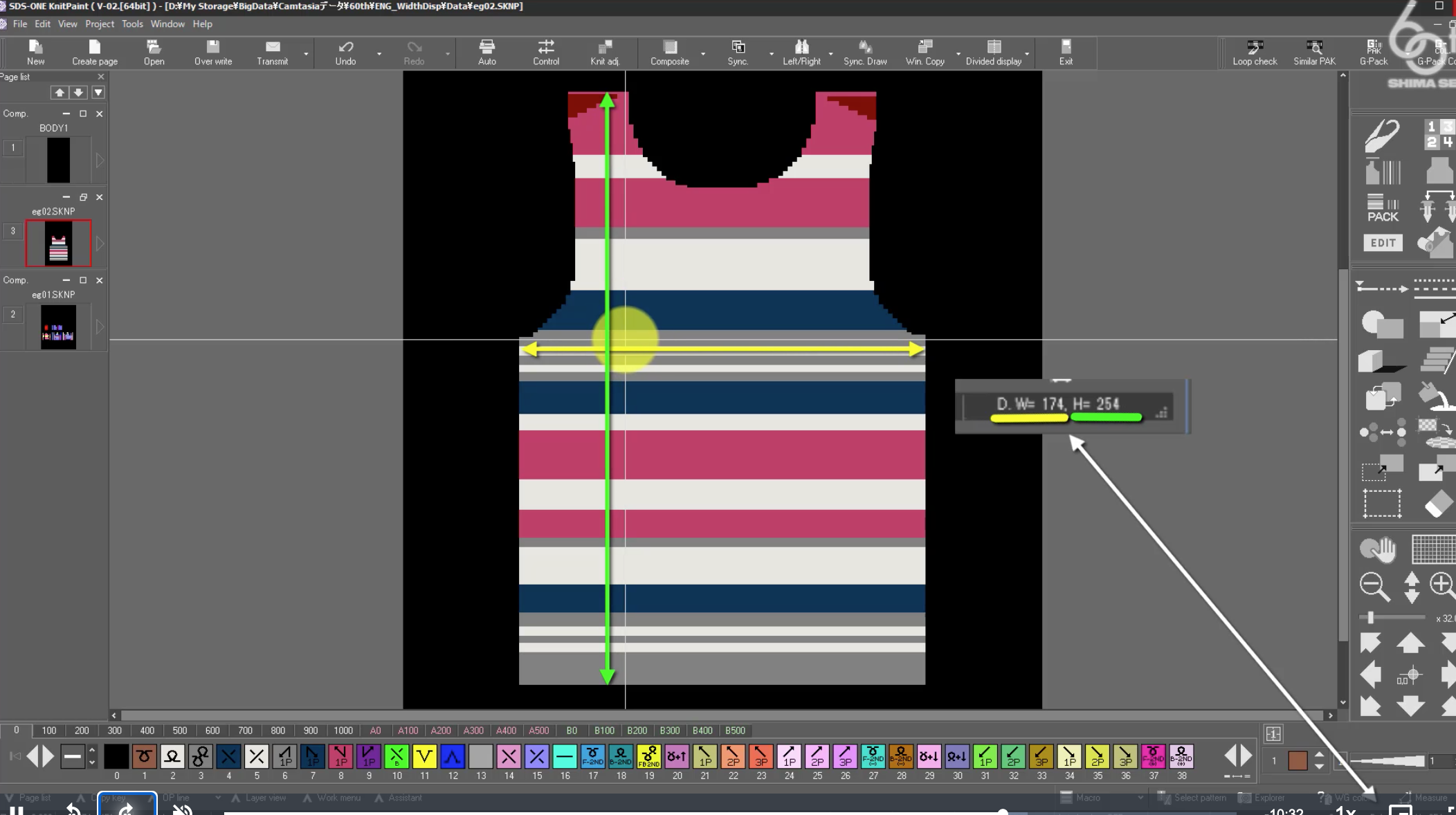
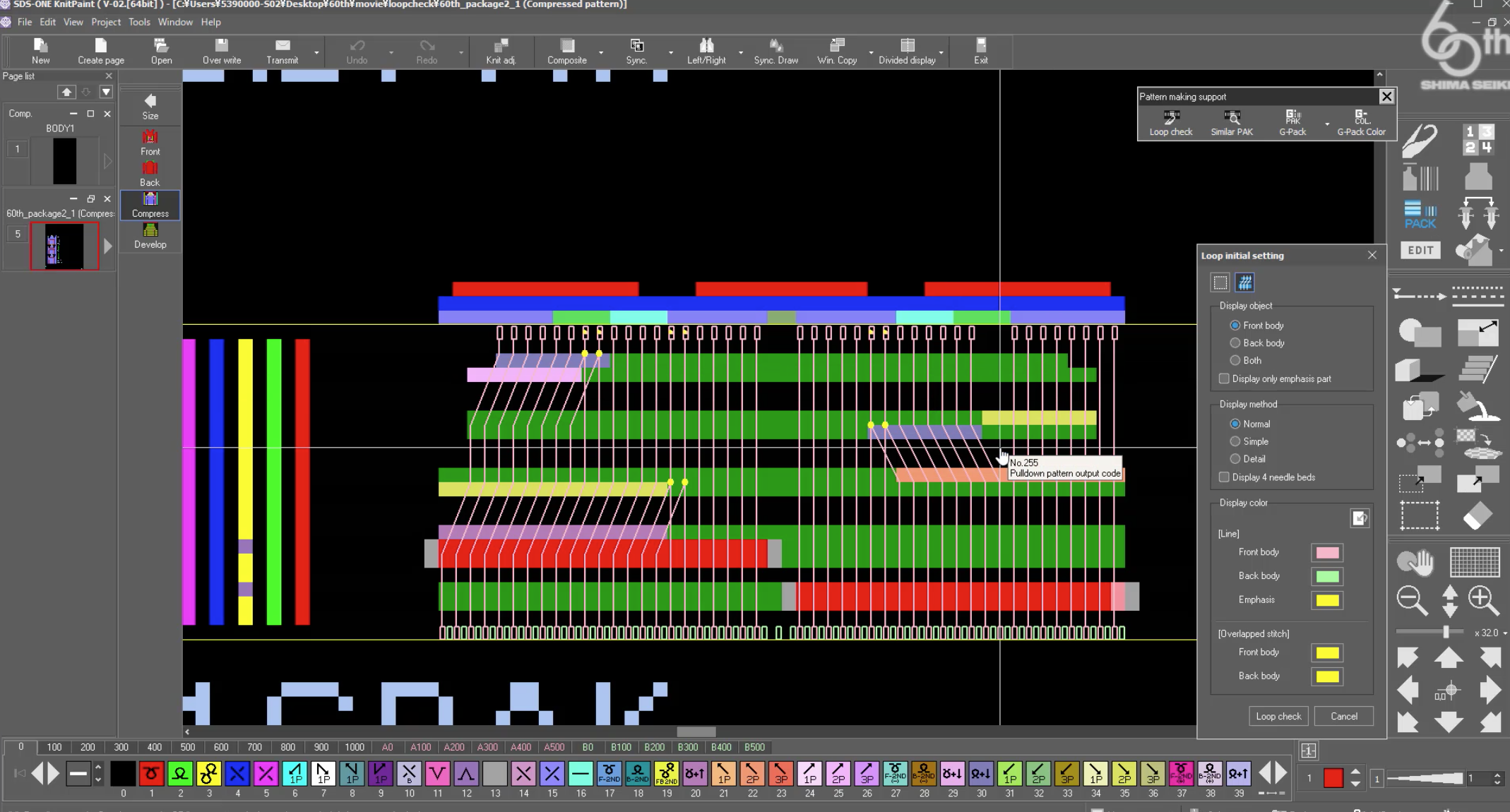
Design system capabilities were highlighted within their video ‘Digital Revolution for knitwear: realisation of DX from product planning to product’. This showcased how Shima Seiki software can impact many channels within design, manufacturing and production.
Here, Shima presents an alternative to conventional workflows.
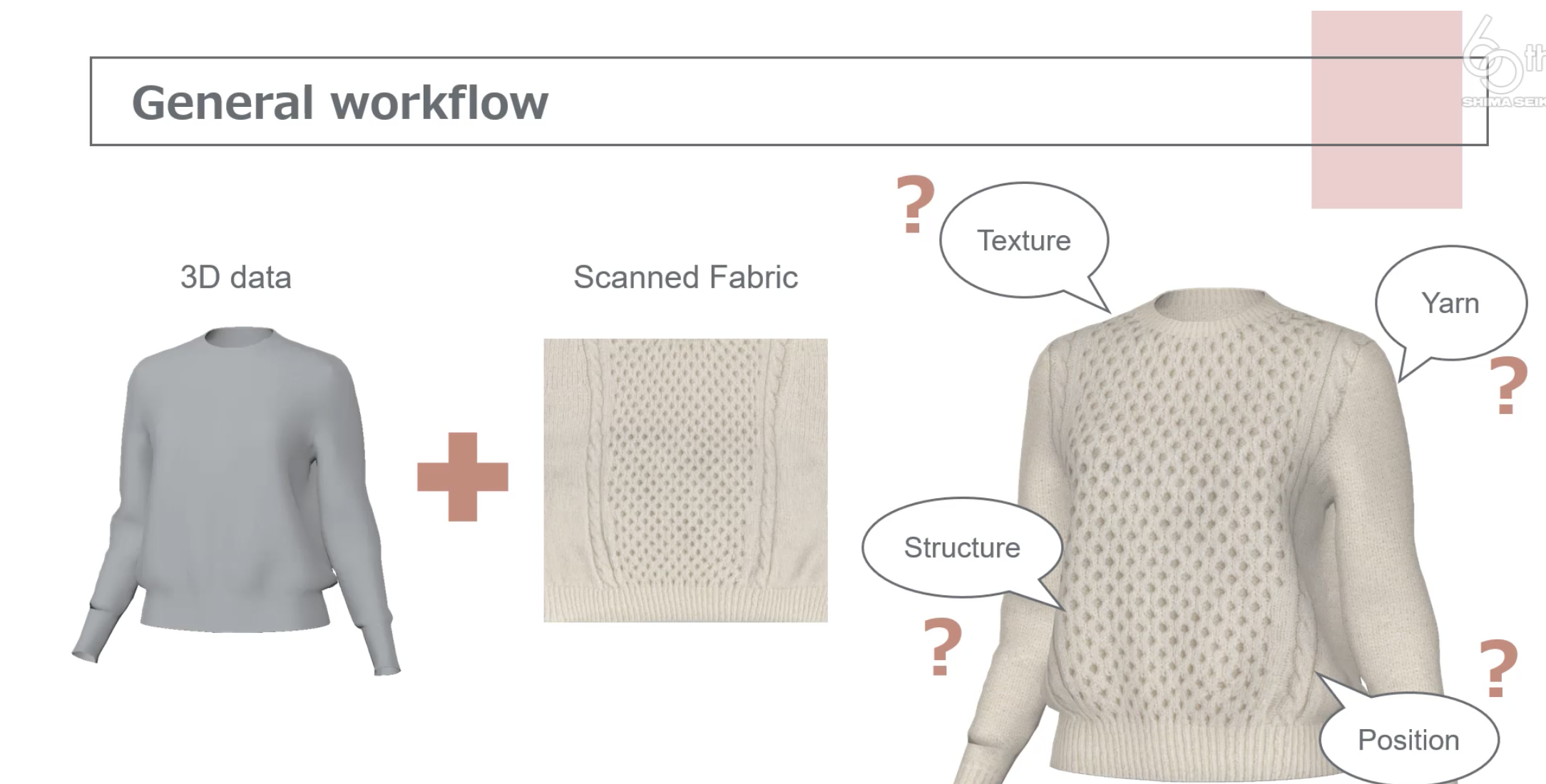
Intentions and communications are not necessarily clearly communicated within conventional specs and technical instructions. This can lead to material waste, delivery delays and higher development costs. Shima’s virtual 3D sampling technology has been advancing to create more ‘concrete’ images of products which can be used to communicate design intentions.
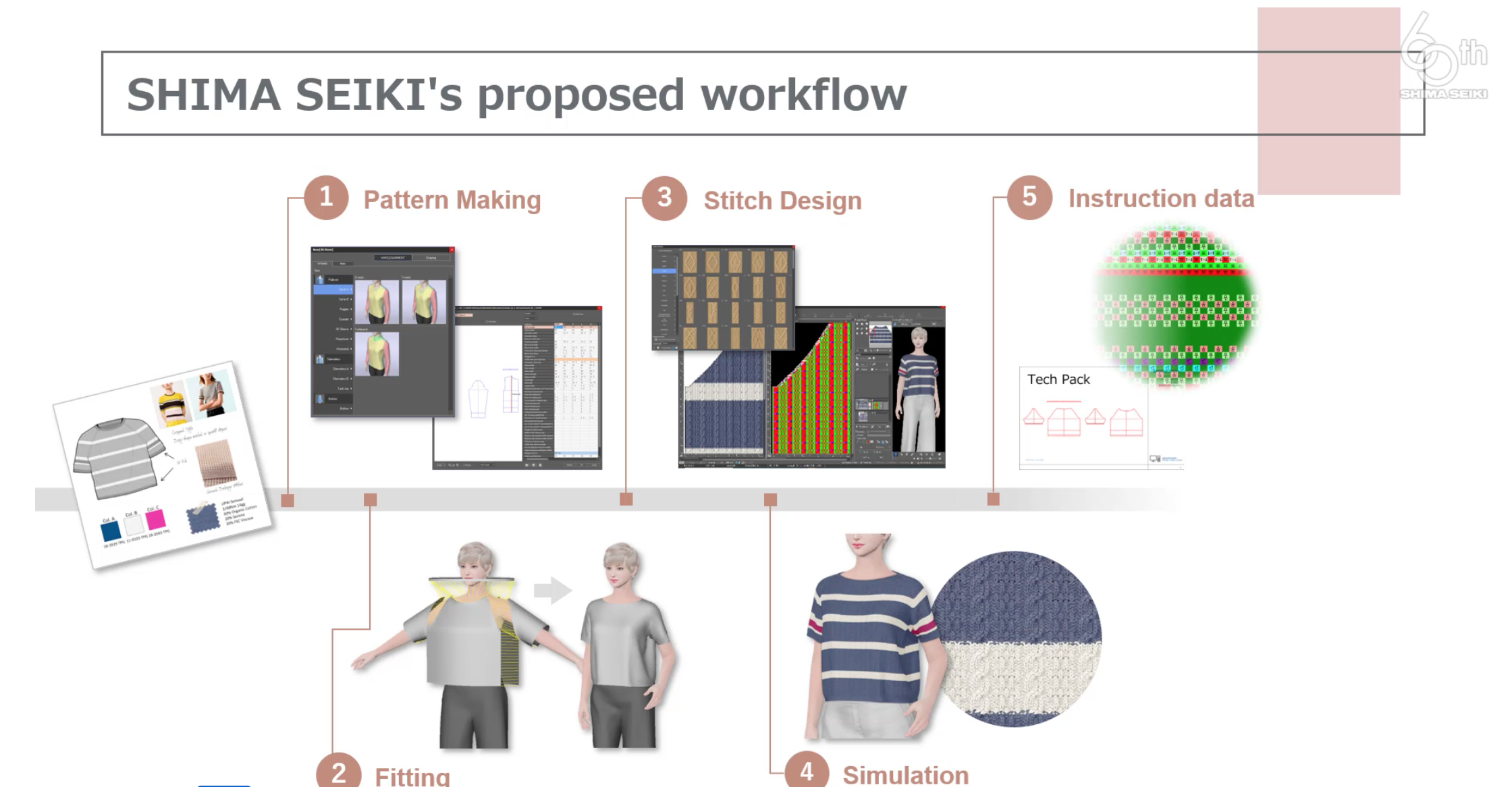
Shima’s proposed ‘Digital revolution of knitwear’ raises three key points: quick data creation using Shima Seiki Online services, design confirmation with realistic virtual sampling and creating knitting data efficiently, passing data directly to factories. This, Shima argues, could drastically improve accuracy of samples and reduce material waste in product development.
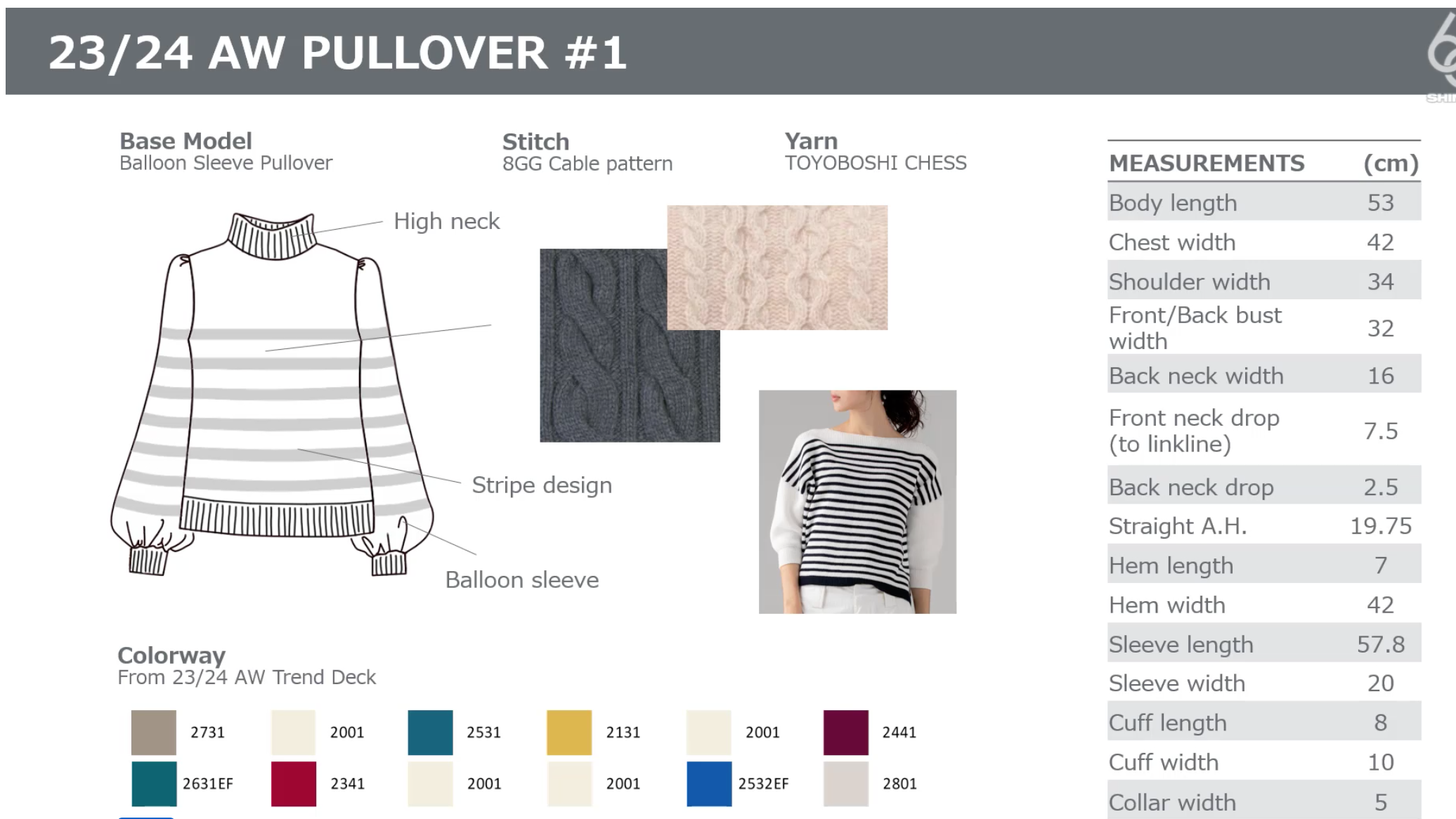
The capabilities of Data Mall were also demonstrated.
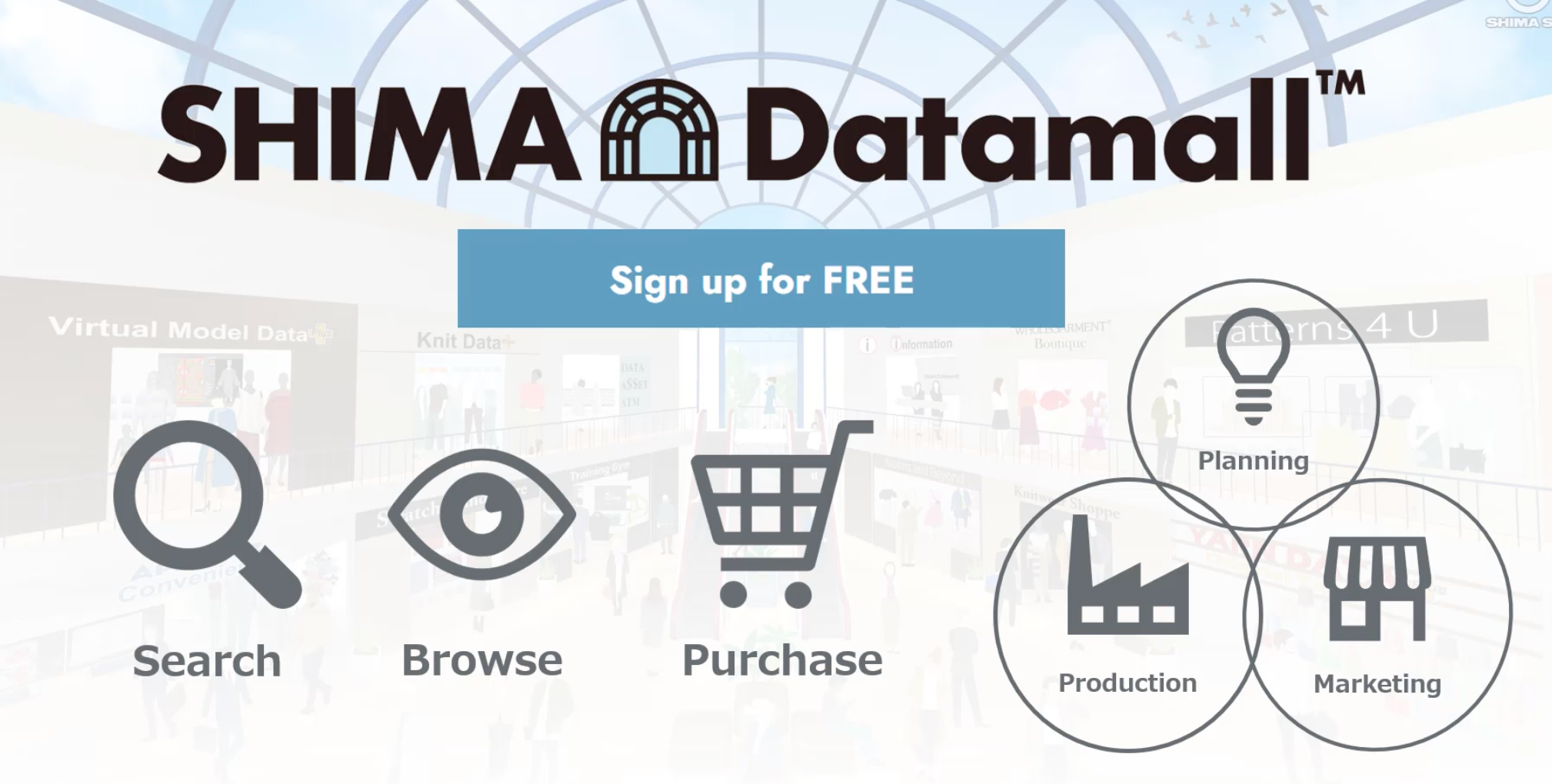
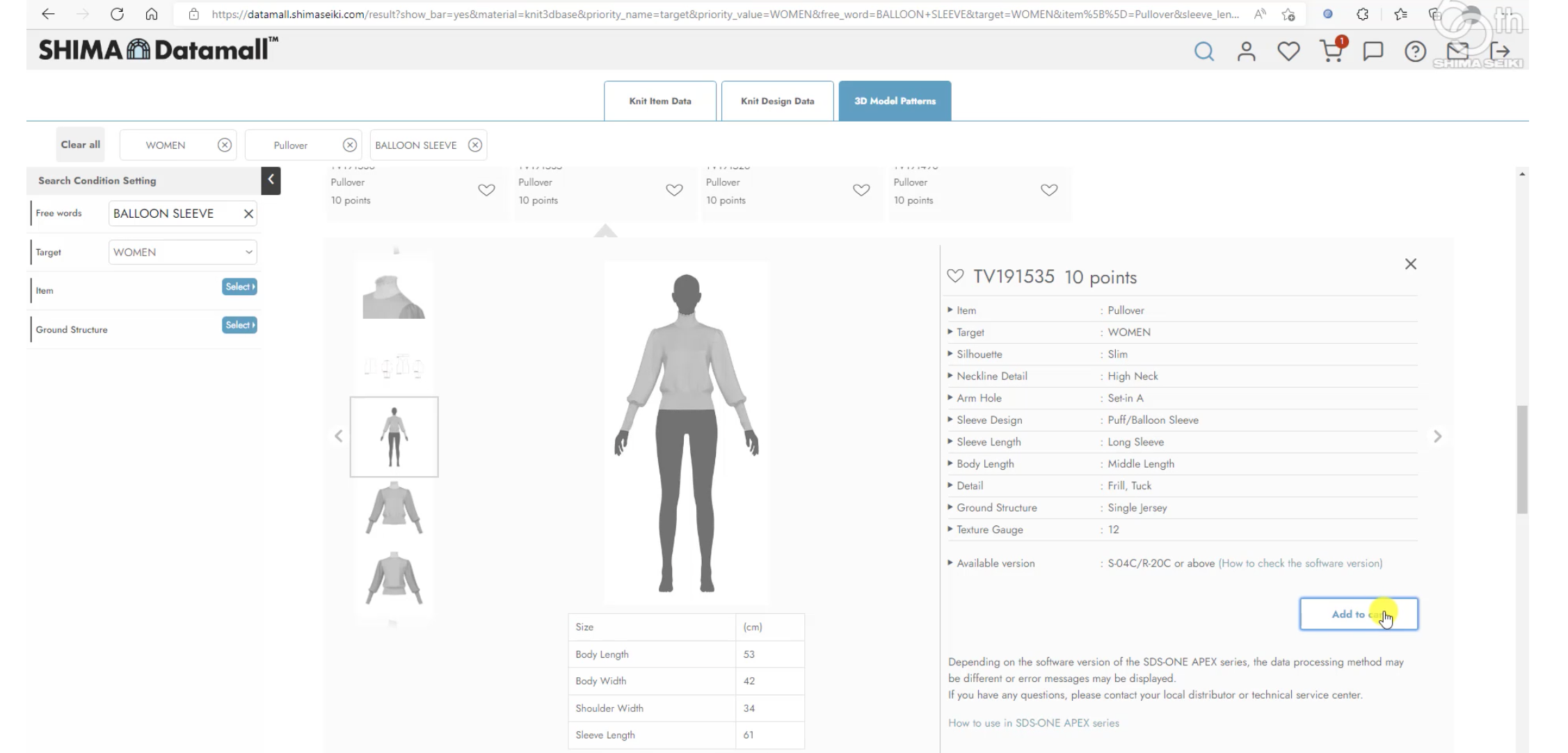
Rendering 3D samples using exact yarn and fabric information is one of the many exciting elements of Shima’s software. To share how easily this can be done, preparation of material data was demonstrated in another of Shima Seiki’s celebratory video offerings, ‘Accelerating digital fabric sourcing for 3D production creation’.
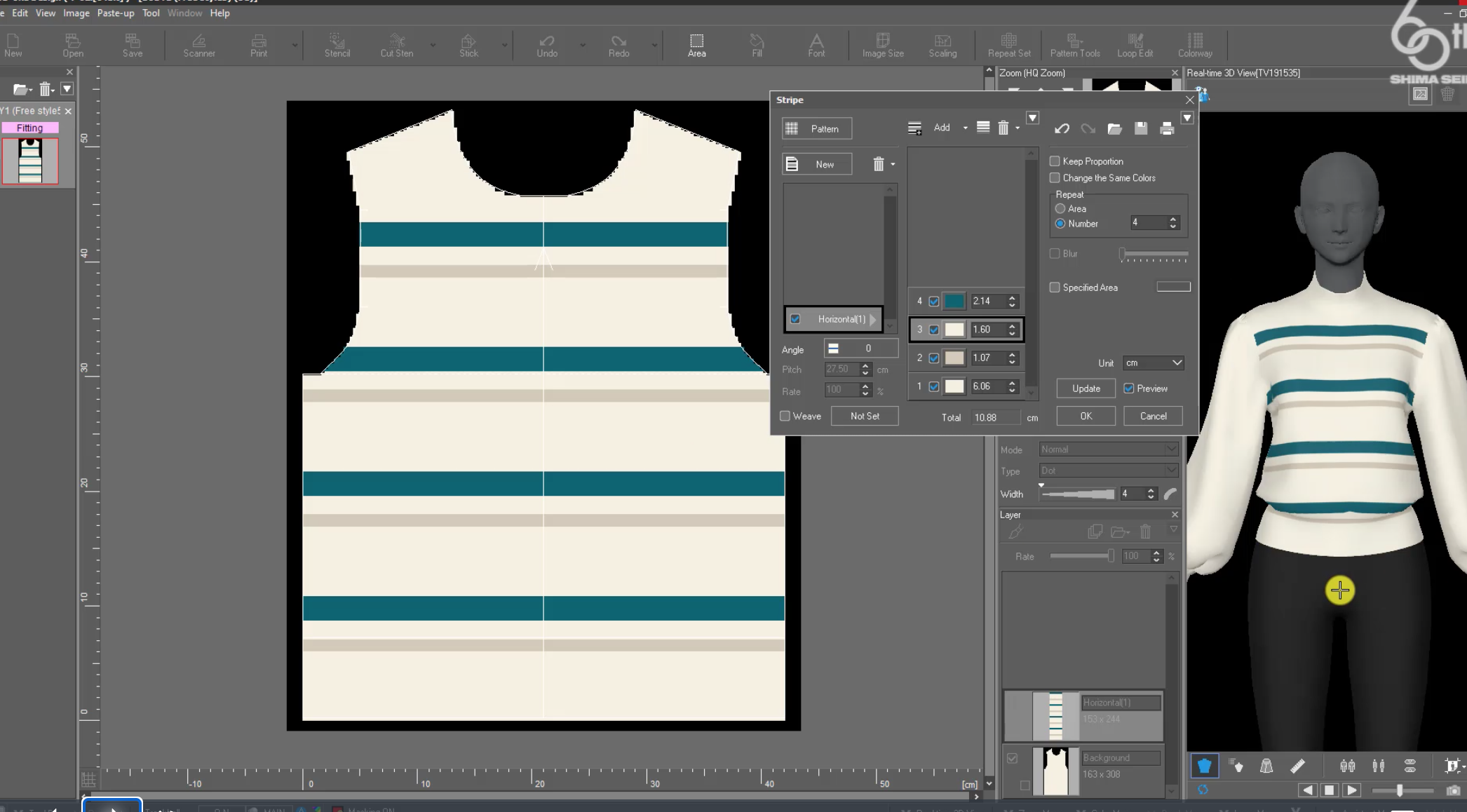
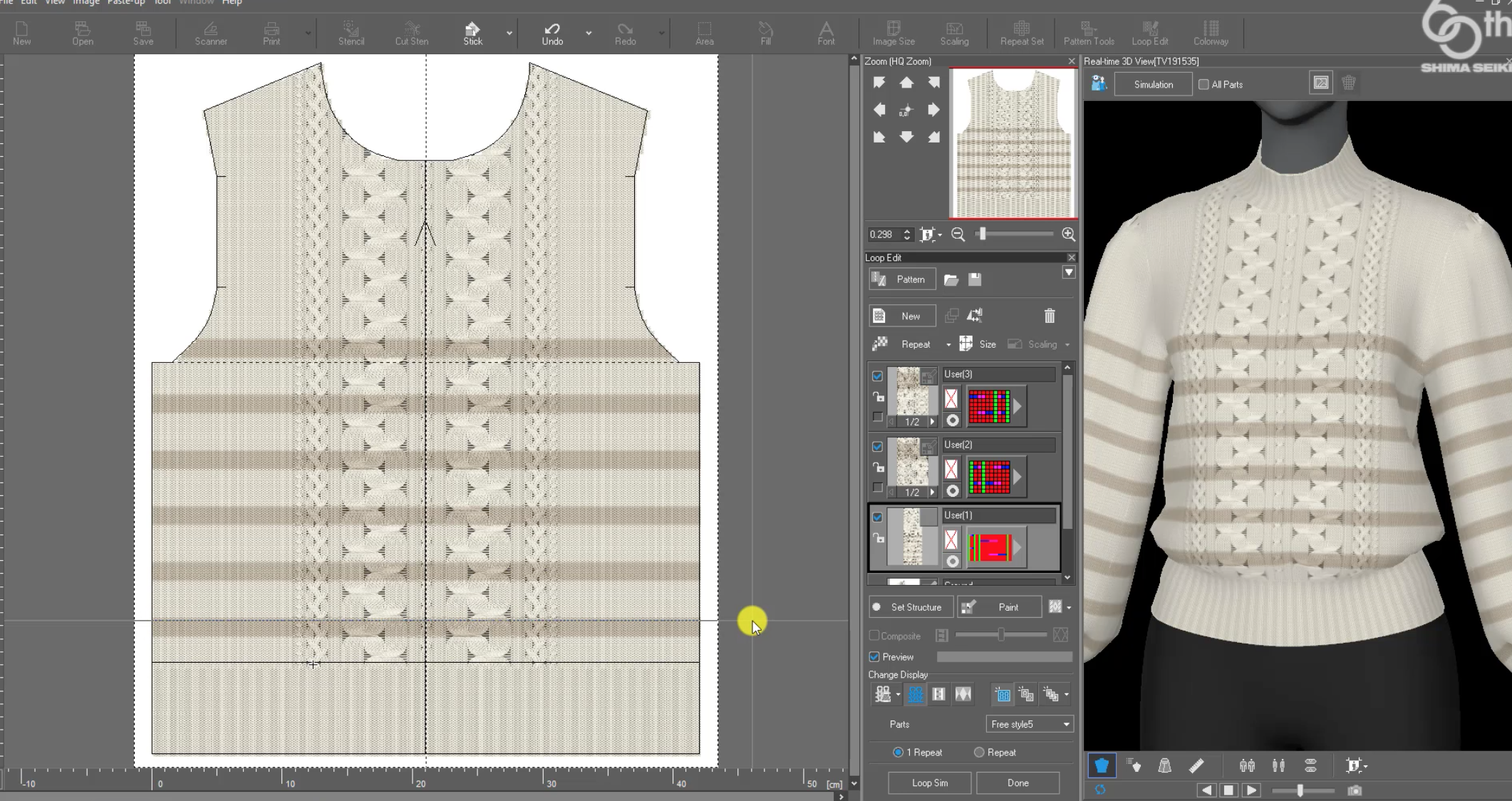
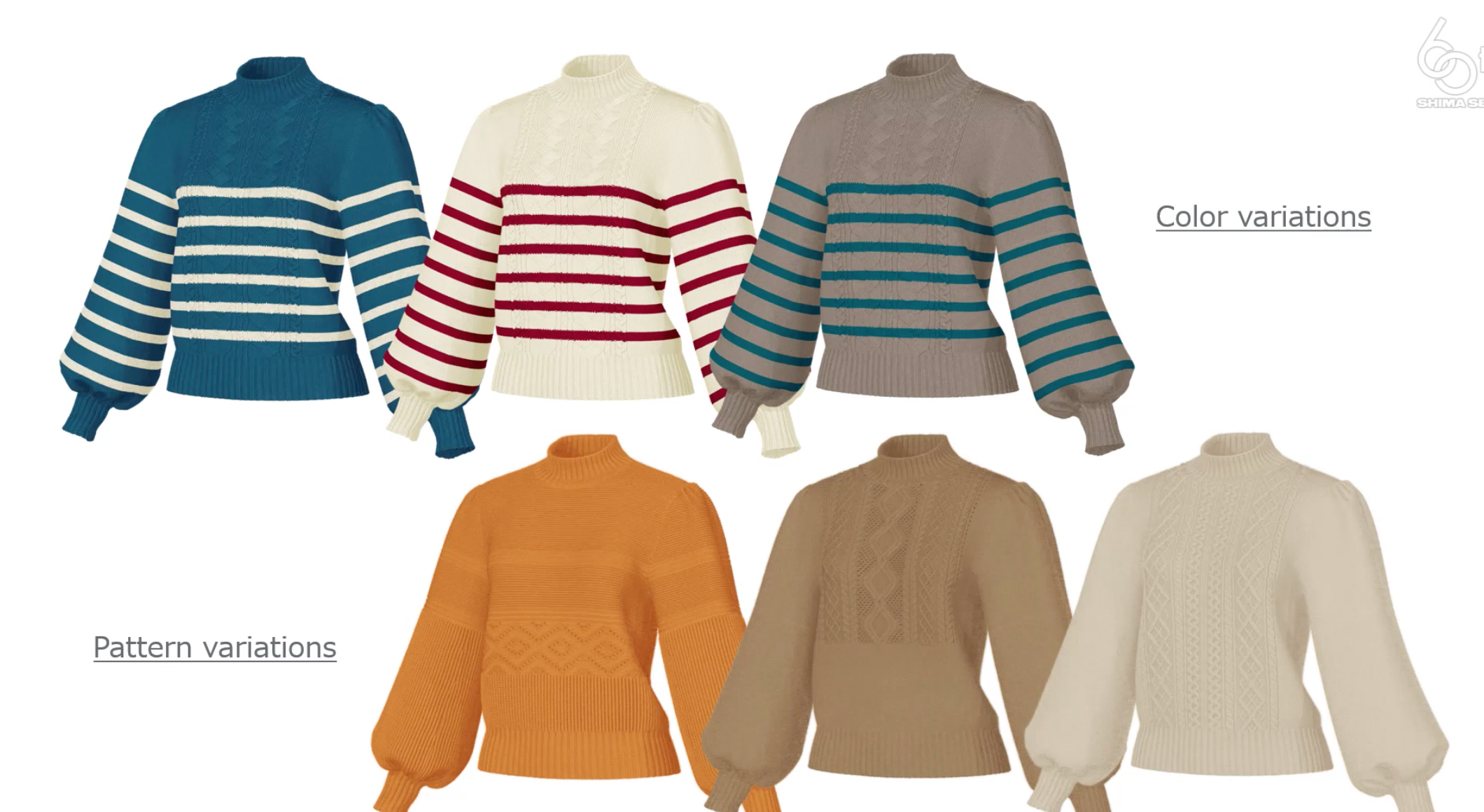
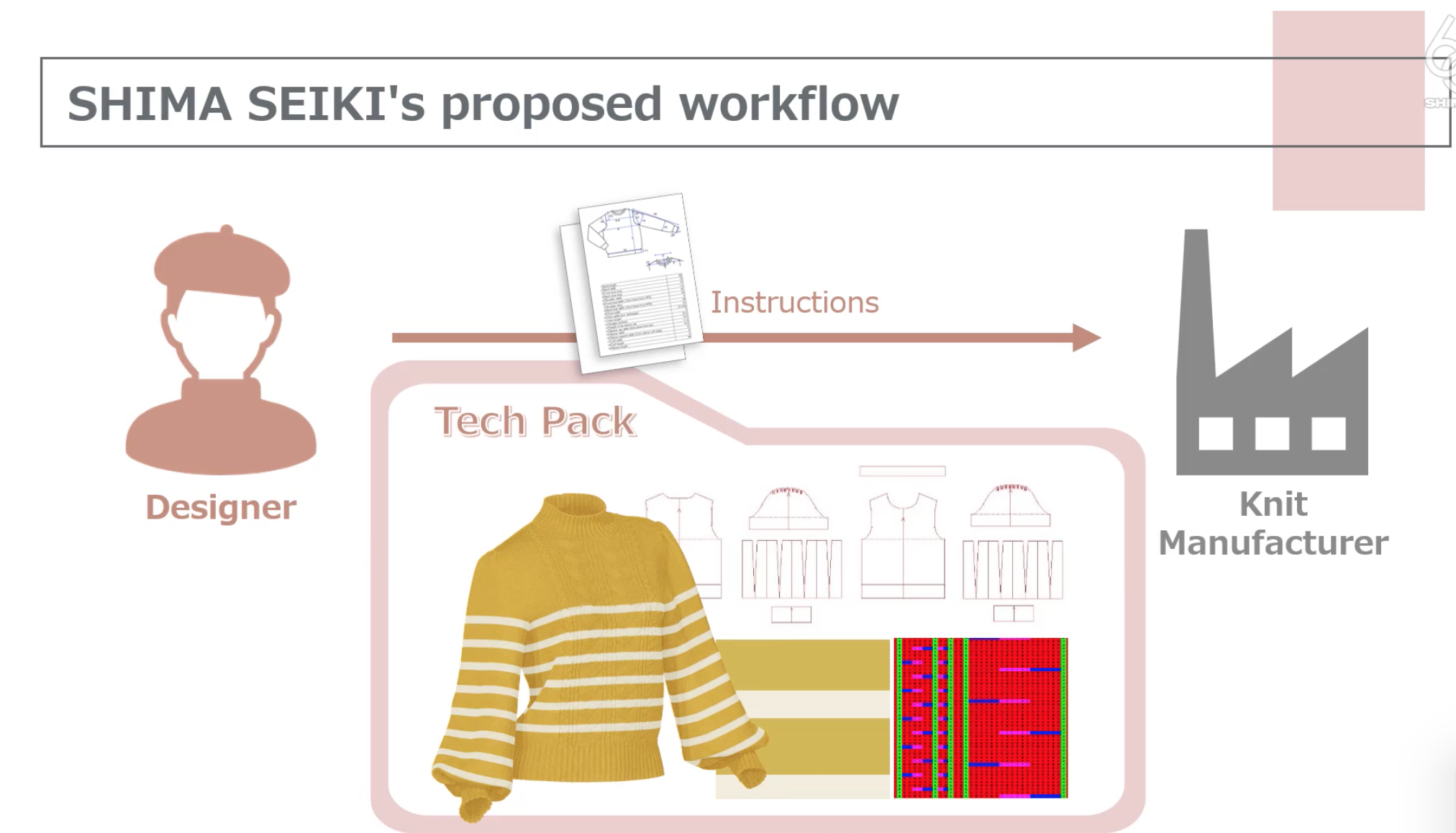
To apply a fabric to a 3D rendering, a physical swatch is usually relied upon to create a texture map. Users can scan in a fabric that they already physically have, and this scanned fabric is captured. A repeat pattern can then be automatically set from this image. However, if a user has a new fabric idea that has not yet been physically sampled, they have nothing to scan in. Shima’s video offered a solution to this problem.
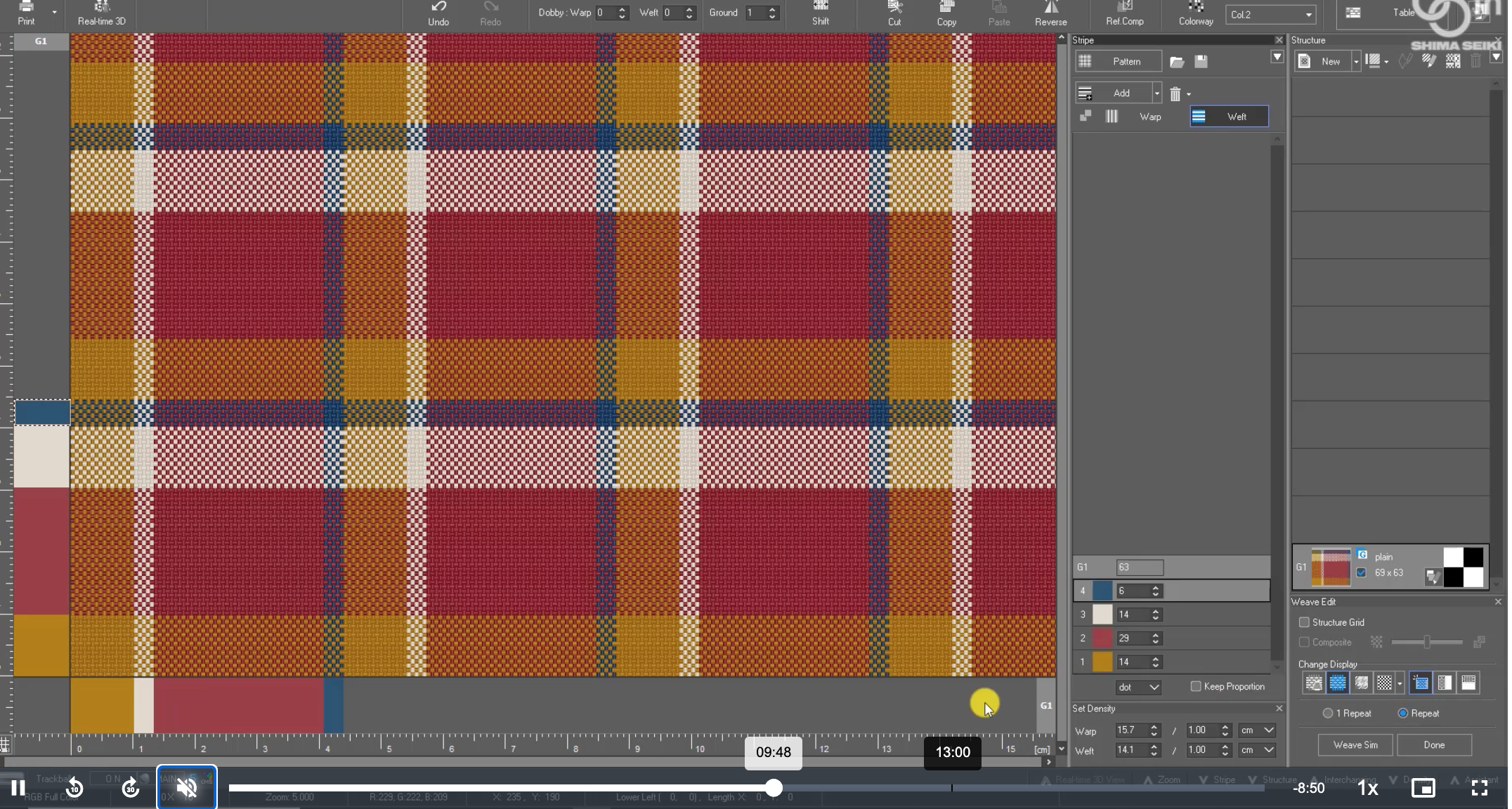
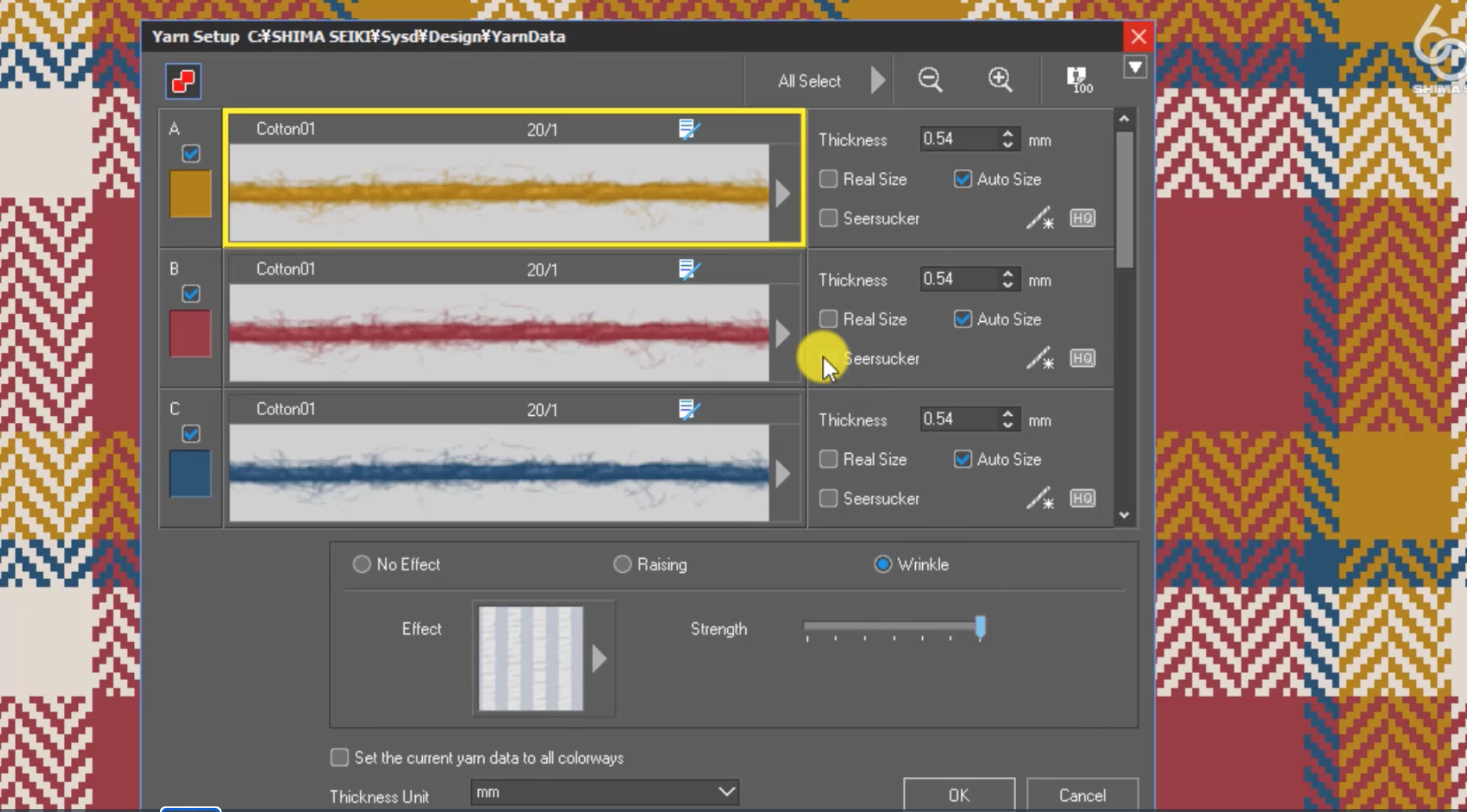
For developing new patterns and designs, lead times to get samples impact delivery dates. Producing yarns, arranging looms, weaving and finishing fabric samples delays production. Digital production of new fabric ideas removes these lead times and allows users to 3D sample in fabrics that do not yet exist physically. Shima has a library of fabrics that can be edited as a starting point, but users can also create their own fabric designs from scratch. A demo within Shima’s ApexFiz was shared with viewers in this video, showing how quickly users can visualise new fabrics ideas – quickly editing colours, yarns, textures and patterns.
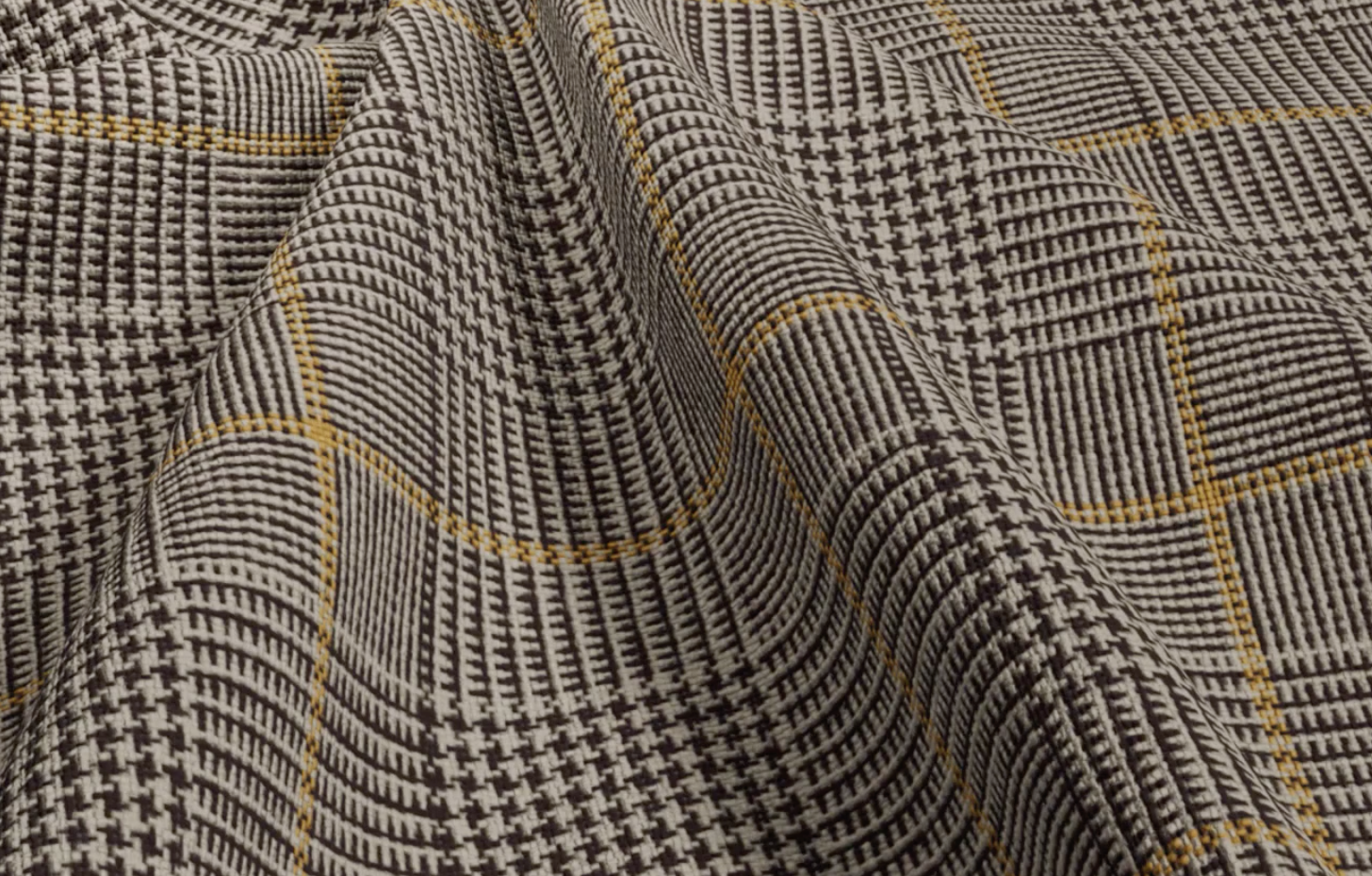
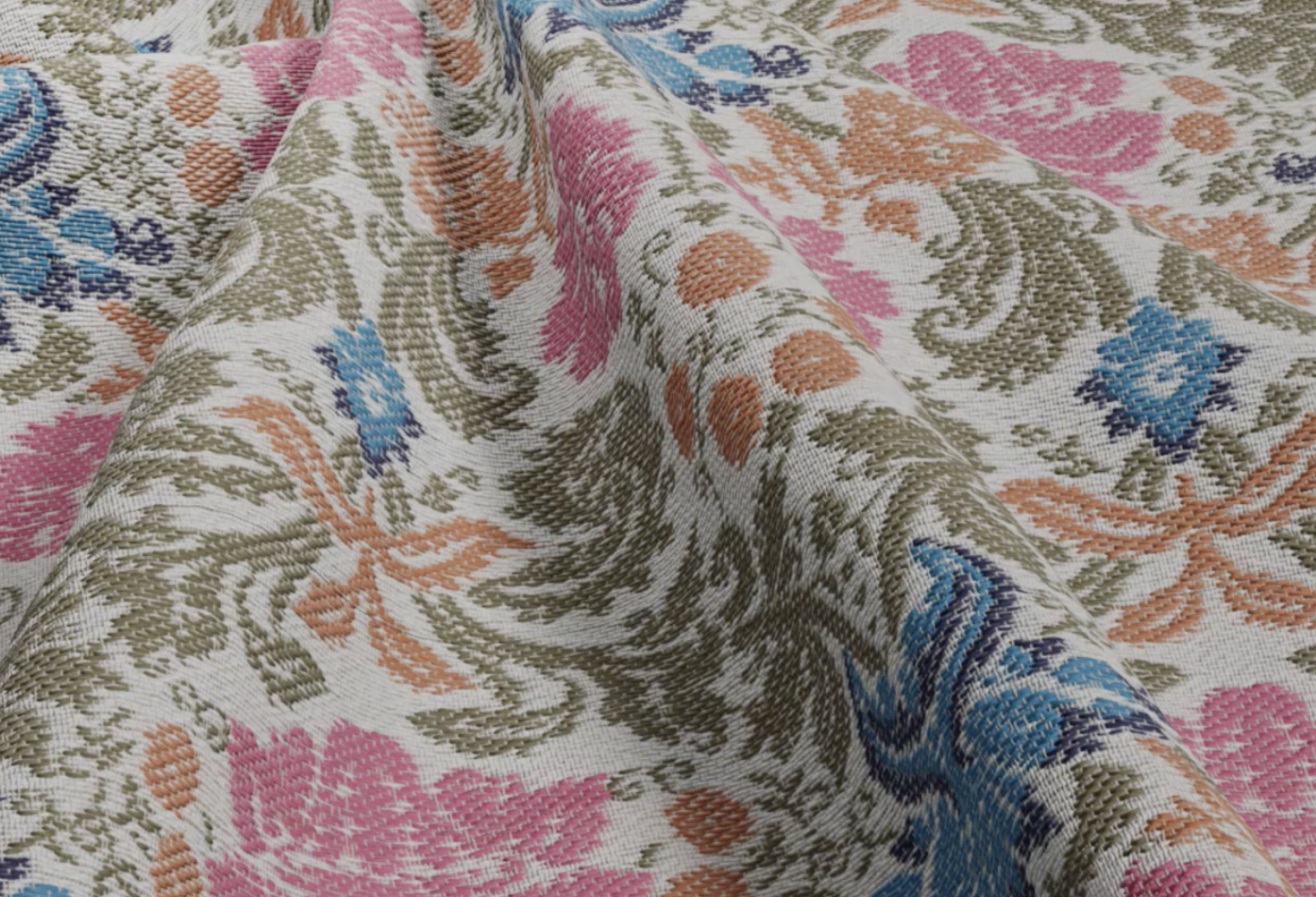
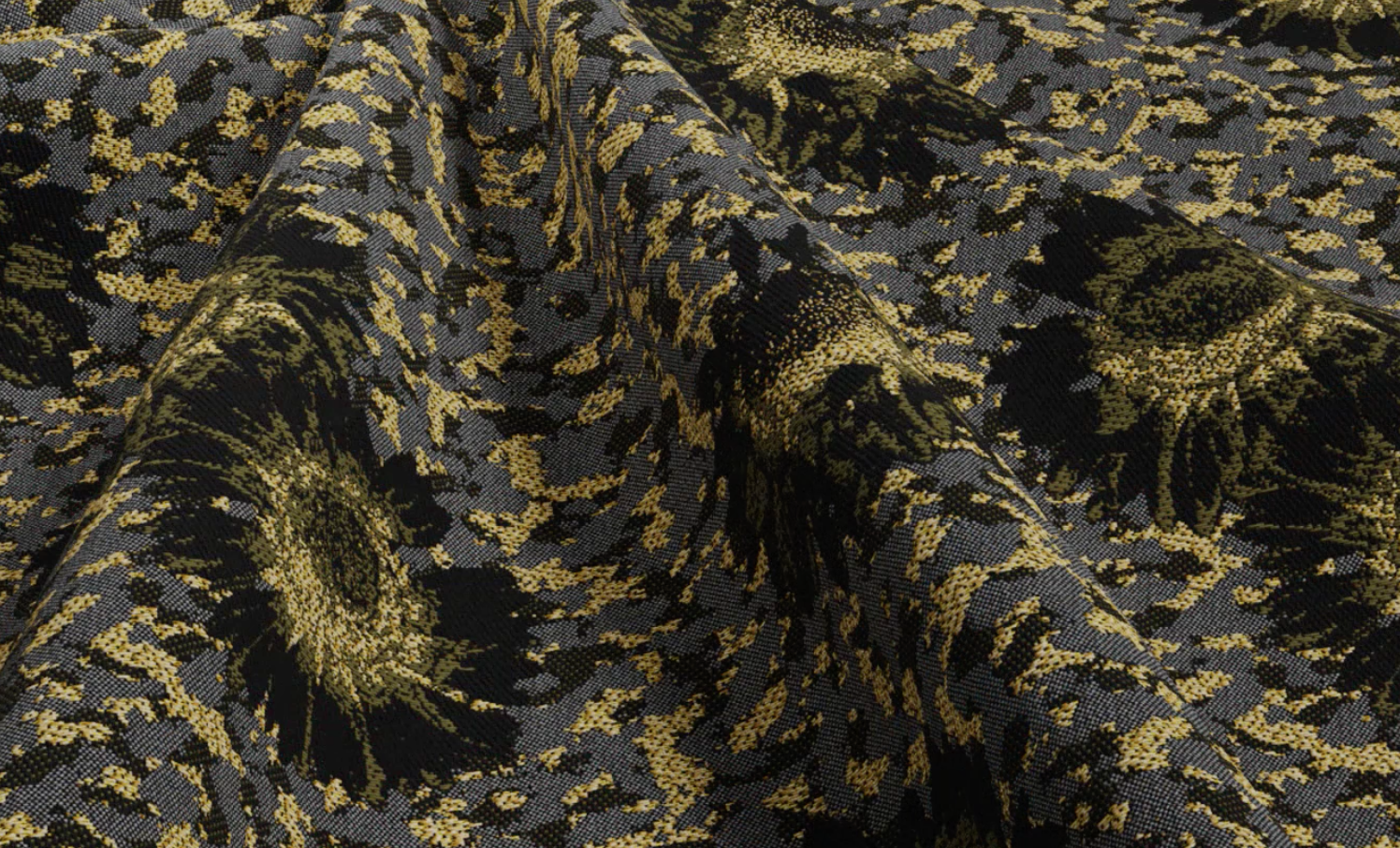
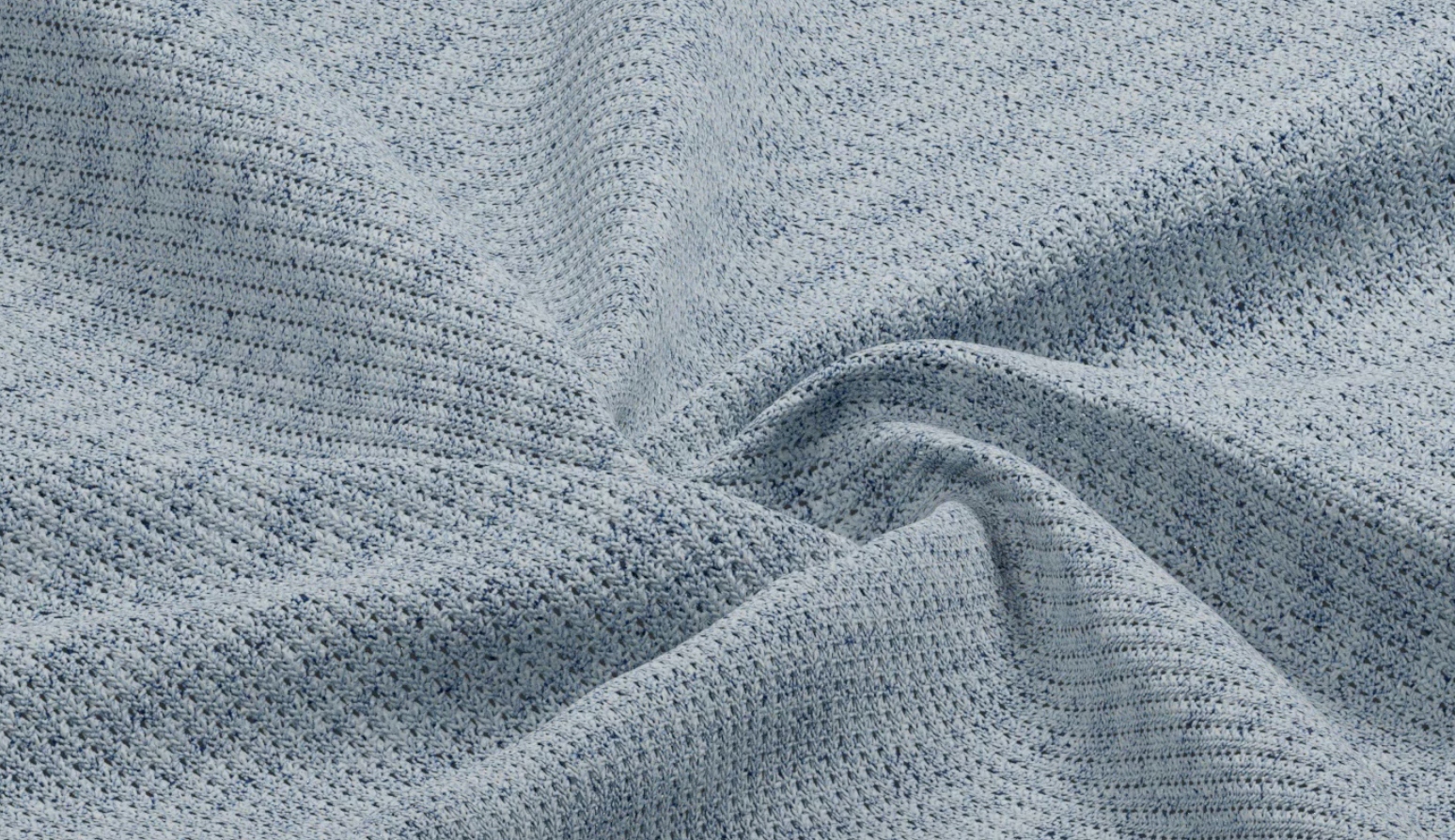
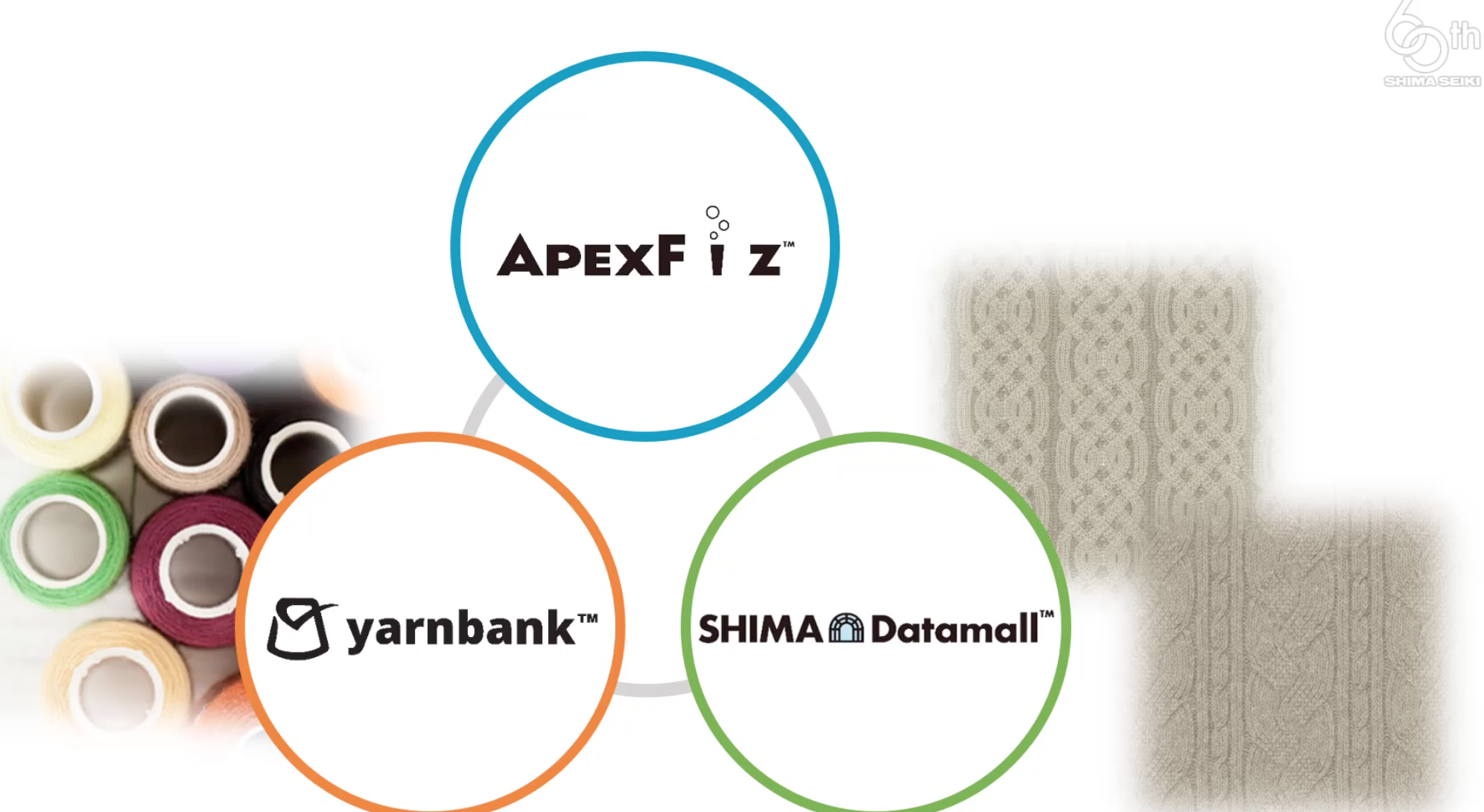
Shima also shared videos as part of their celebration introducing some of their newest machinery developments.
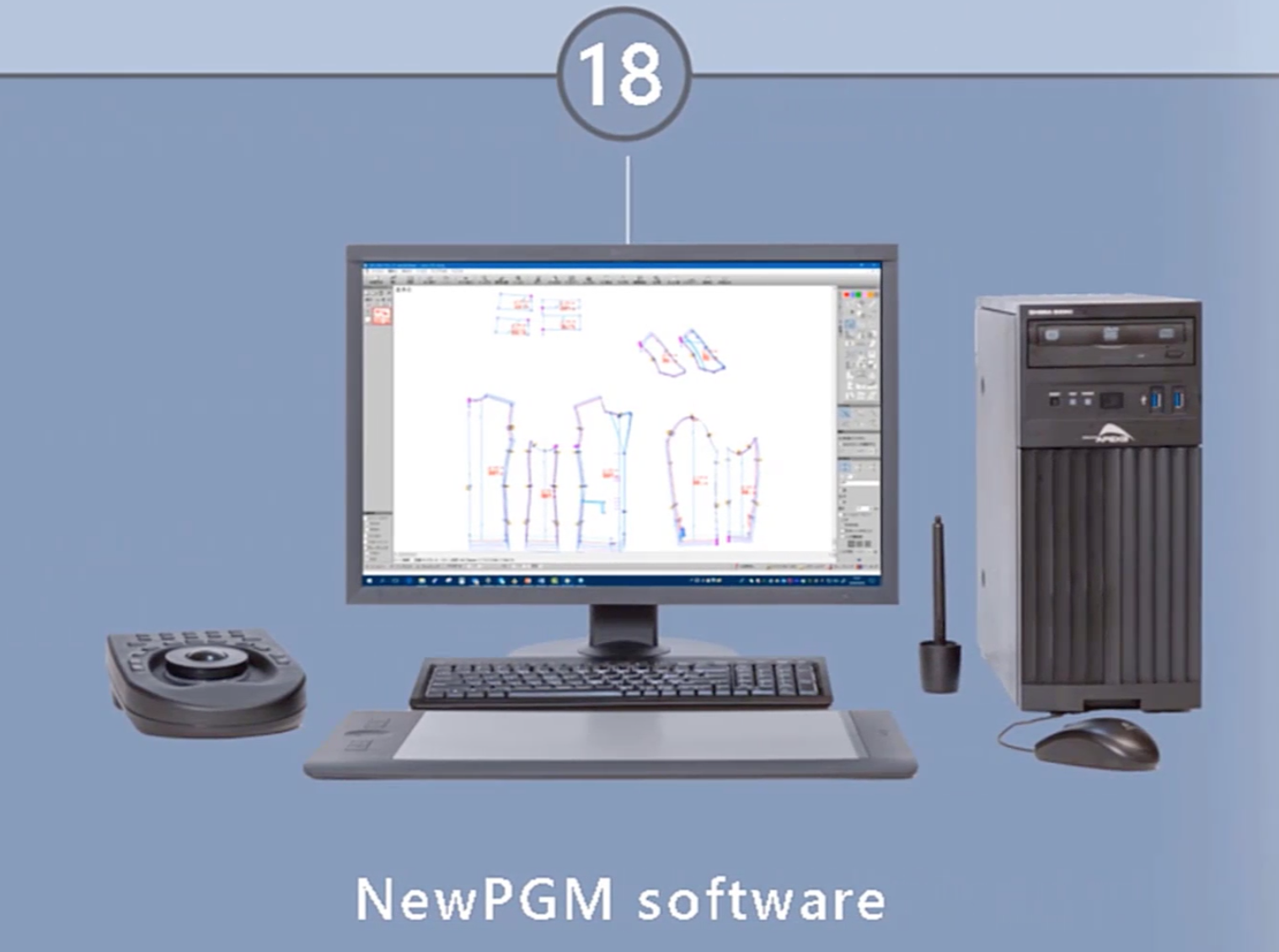
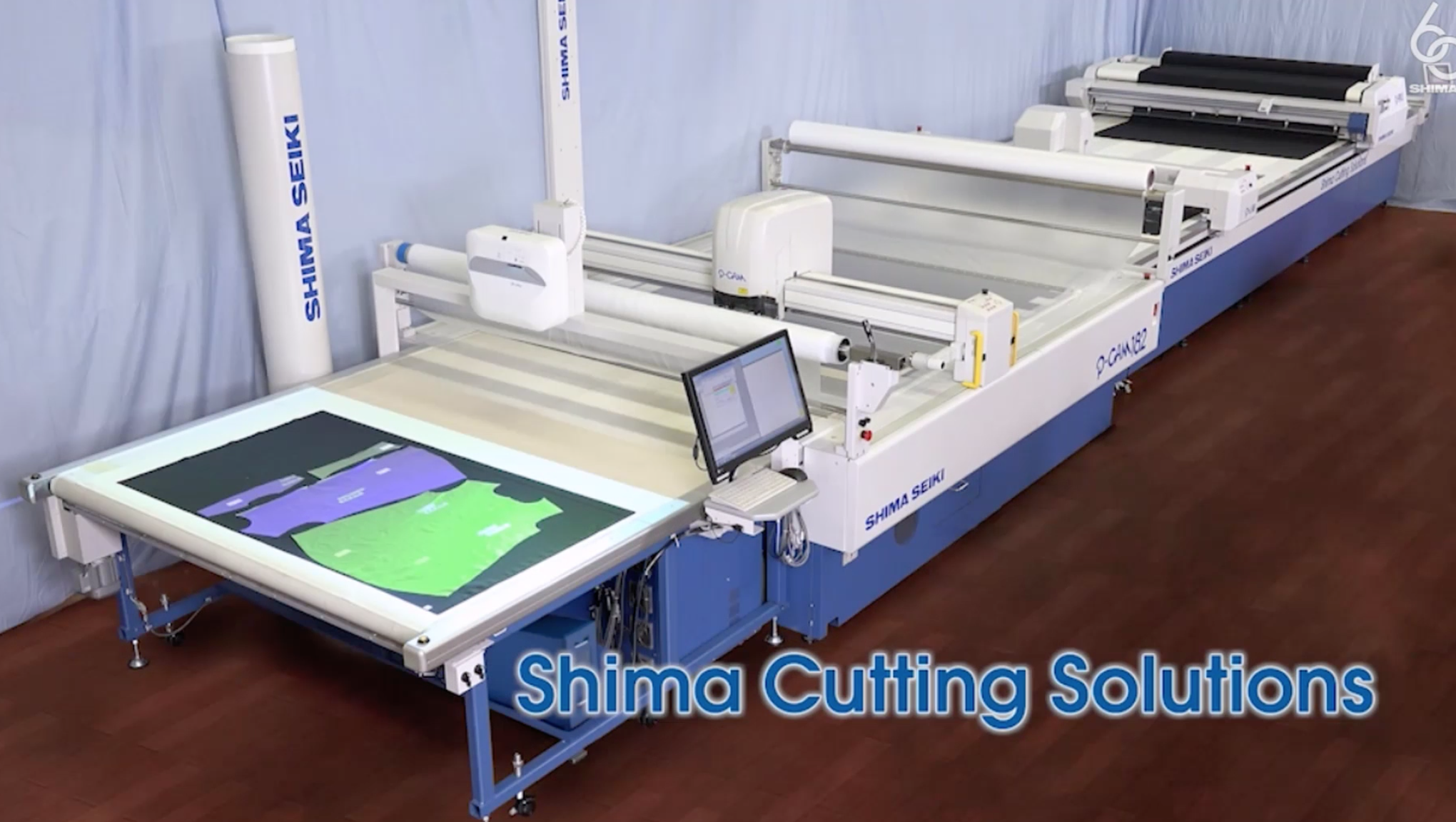
Shima cutting solutions that combine spreading, labelling and cutting were shown, as well as Pattern Matching Premium, a CAM specialised for repeat pattern matching. The P-SPR2 automatic spreading machine was demonstrated within the video too.
Efficiency was exemplified by this machine in numerous ways. Selvedges are automatically aligned and spread for optimal cutting and the marks indicating blemishes are detected and avoided. The machine automatically returns to the required location to continue spreading, preventing shortages of fabric. After spreading is complete, the origin label is affixed. Shima cutting solutions automate cutting workflow by detecting the original label at each step. Part numbers can be affixed on labels to the pattern pieces which facilitates the sorting of the pattern pieces whilst minimising chances of mistakes.
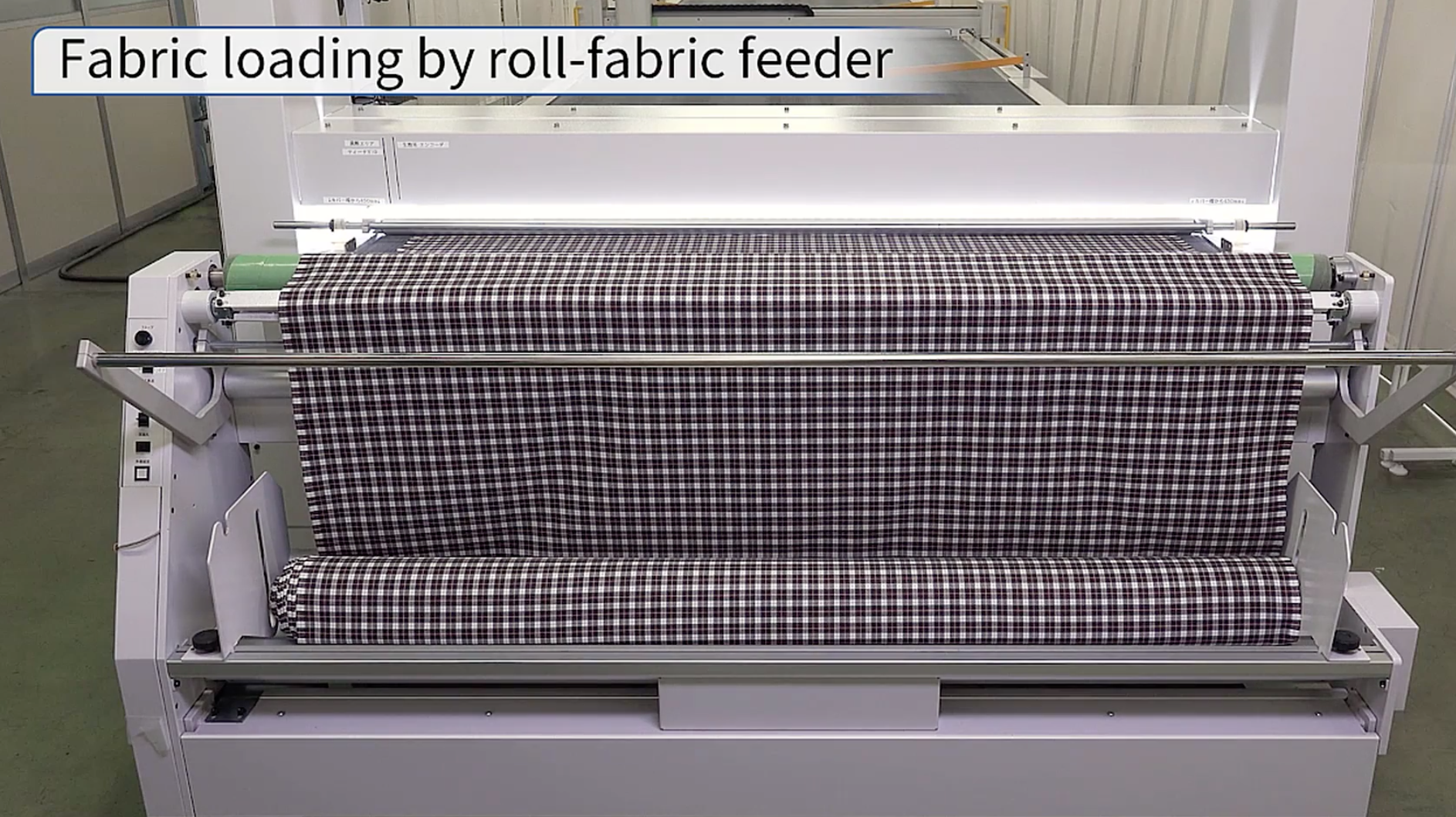
Shima’s automatic cutting machine with pattern matching capability leads fabric onto a conveyor, reads the position of the pattern with a scanning camera and auto adjusts the marking data according to the fabric pattern.
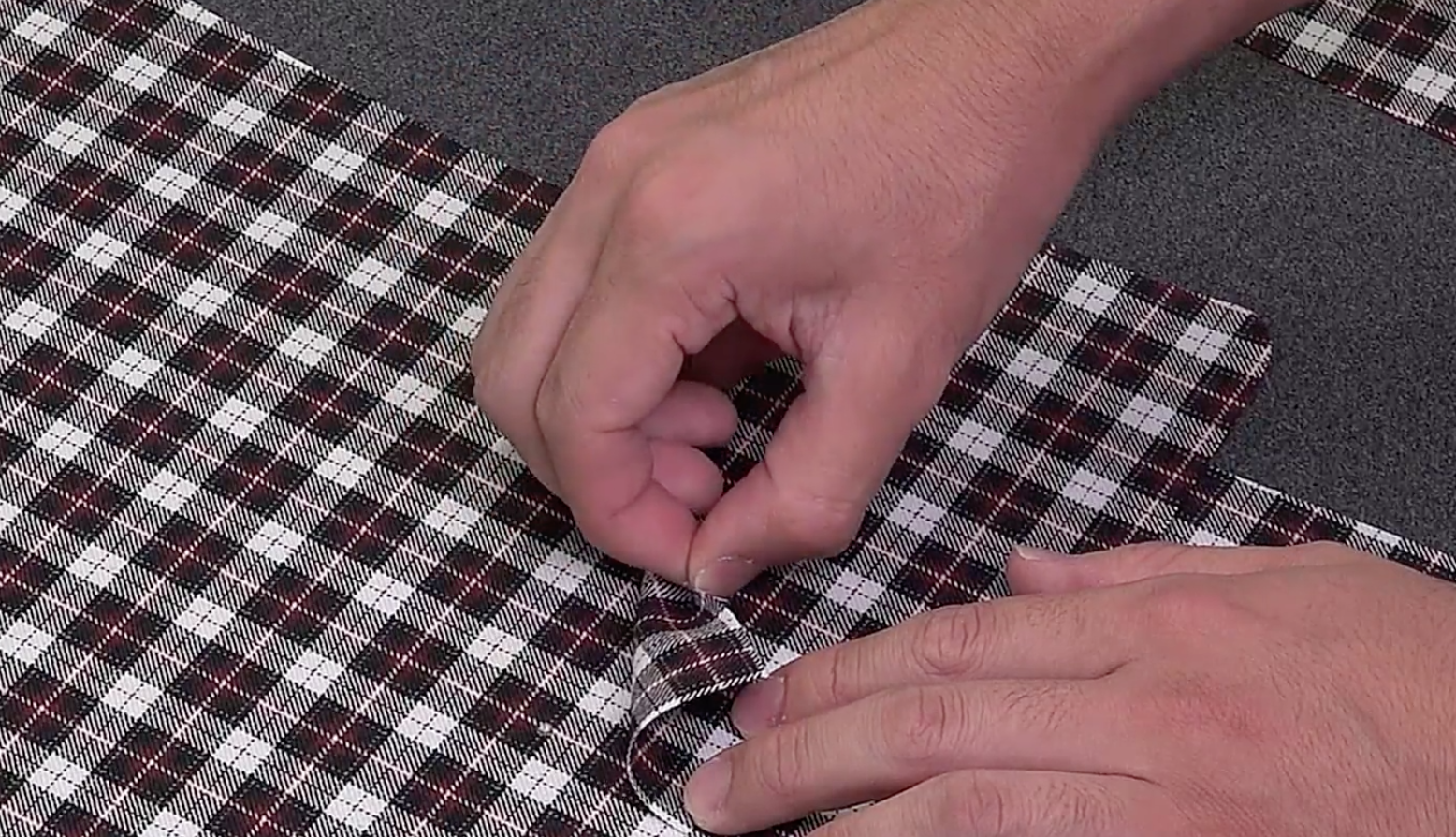
Pattern matching can be time consuming but with Shima’s technology it can be completed in an instant. The scanner reads the pattern and the cutting results in hems and all sewing parts matching up in their patterns.
When fabric passes through the scanner it is read and converted into data. Distortion of the scanned fabric is graphed and marking data is adjusted accordingly. All marks are adjusted at the same time, removing the need for manual work. When auto pattern matching is complete the data is sent to the cutting machine. Once the fabric is in the cutting area the scanner takes a new image and then the cutting takes place, uninterrupted. This creates efficient cutting as these things happen simultaneously and the time needed to realign mismatched patterns is removed from the process.
When combined together or used separately, 3D sampling of new woven fabrics alongside this pattern matching technology could drastically reduce lead times and material waste.
Finally, Shima presented their video ‘Promoting smart factory in knitting factories’. Shima KnitMAN is a new technology supporting this, created for those who are experiencing problems such as delays in connecting USB data to knitting machines, incorrect data loading and long lead times to collate data.
KnitMAN consists of 3 elements: SPP Shima Production Planning software, SPC, Shima Production Control, and SPR3 Shima Production Report. These three elements combine to alleviate troubles many factories face with data issues. KnitMAN supports the transfer of knitting data and collation of production information from knitting machines, as well as production planning. This software is intended to improve factory work efficiency.
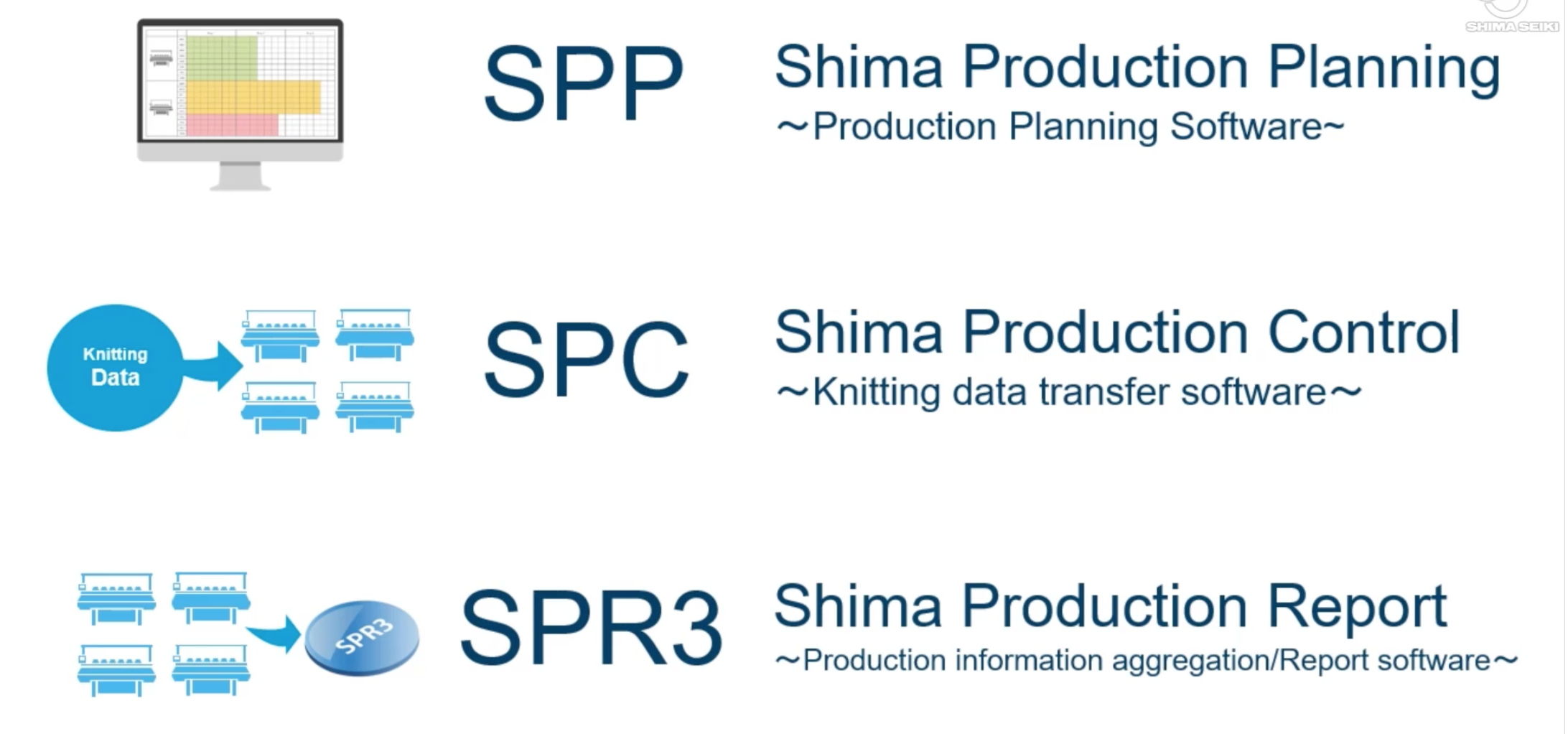
As Shima Seiki enters their 7th decade we look forward to seeing what new innovations and solutions they will present to the industry next. Shima Seiki’s links between their digital and manufacturing technology really are something to celebrate.
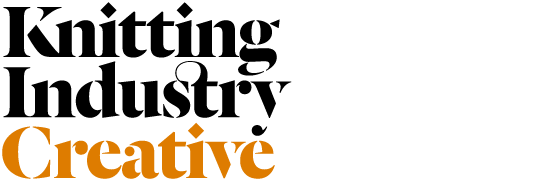
Subscribe To Our Newsletter
Join our mailing list to receive the latest news and updates from our team.