Bournemouth based sustainable knitwear designer Hannah Stote recently took Graduate Fashion Week by storm. Studying her BA Fashion at Bath Spa University, it was only during the summer between second and third year that Hannah learned how to machine knit. Leap forward just one year, and her abilities on the domestic knitting machine are so impressive, she was awarded the Catwalk Knitwear Award at GFW for her sustainably knitted collection. Up against knitters with many years of craft experience, this speaks volumes for Hannah’s commitment to honing her craft in such a short time.
Utilising British Wool and British yarns, as well as unraveled yarn from vintage jumpers, her focus on material choice within the collection was responsible and ethical. Hannah’s GFW collection truly encapsulated her understanding of knitted structures, as well as the value she places in sustainable fashion design.
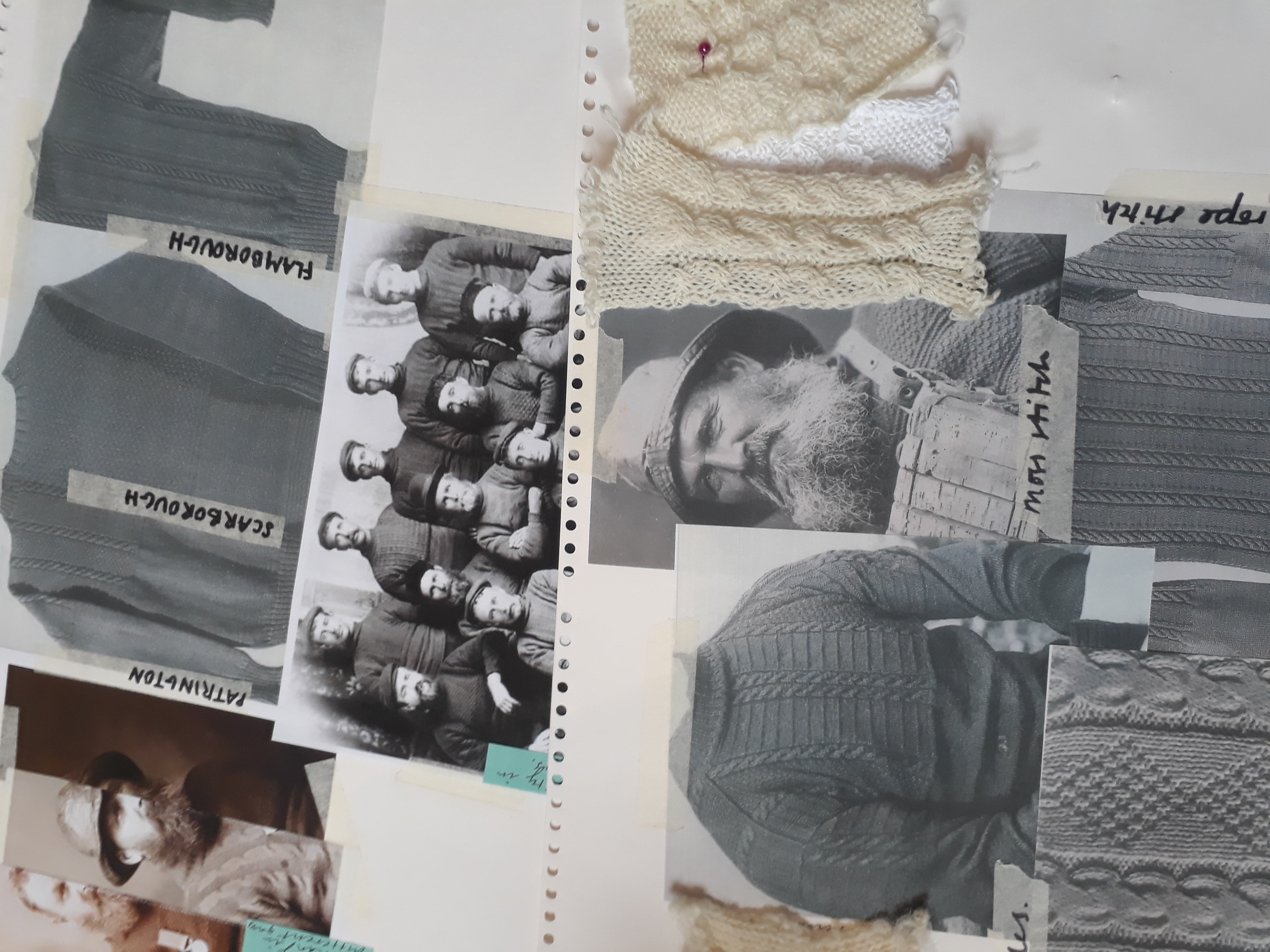
With freedom to approach textiles and fashion in a broad sense within the Bath Spa BA Fashion course, Hannah decided to explore the potential of the domestic knitting machine in the summer before her final year. She took a course in domestic machine knitting and here, her identity as a designer was truly formed.
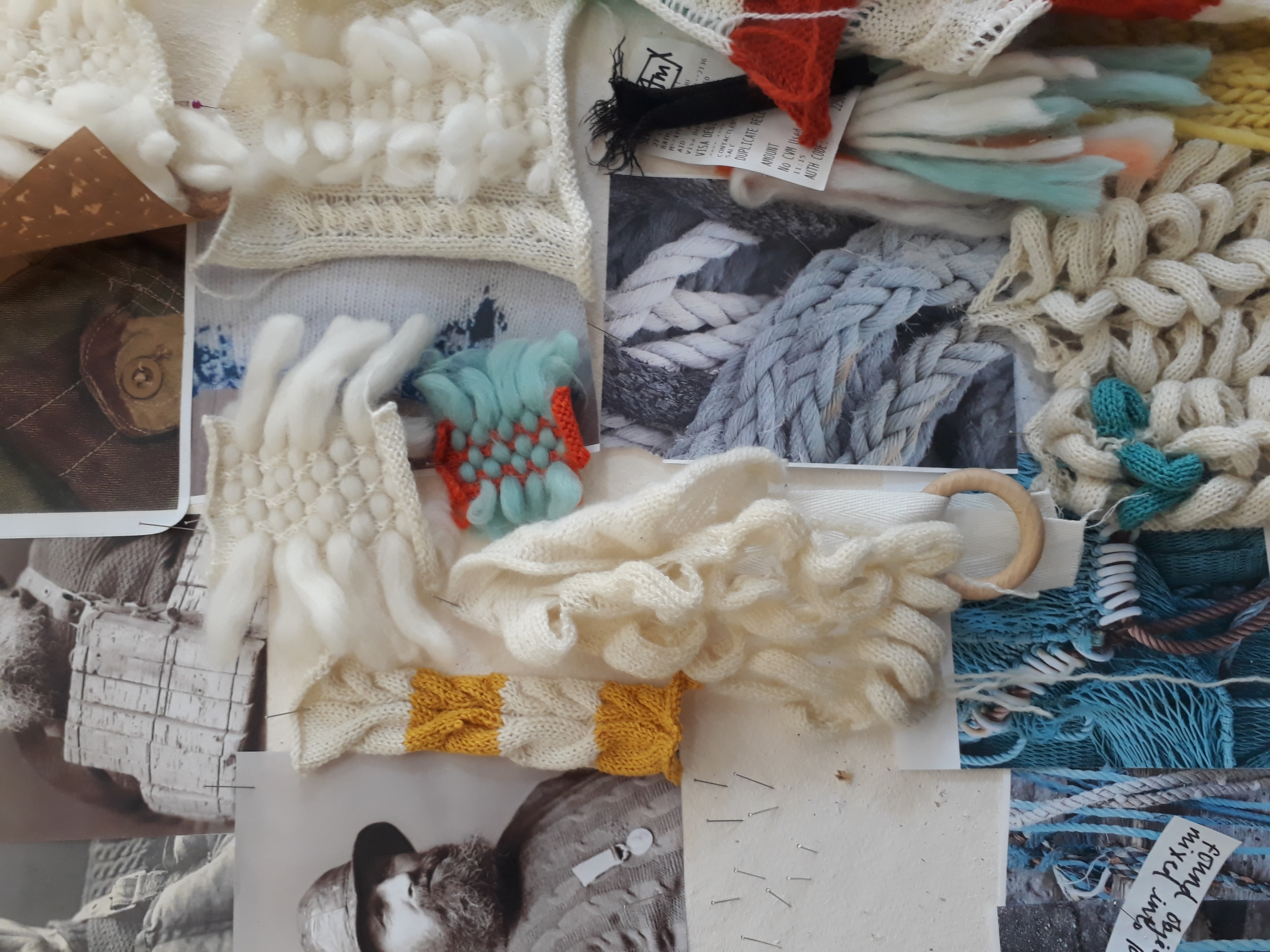
Describing her practice, Hannah reflected, “I believe in conscious and responsible design, so the values of my graduate collection centered on that. I use natural fibres and for this collection I used 100% wool, the majority from British sheep, spun in UK mills. I combined these with fibres sourced from unraveled charity shop jumpers. The fact that wool is a renewable fibre led to my research into how to make my collection fully recyclable – I settled on the fully fashioning method of shaping and chose to use only integral fastenings, like knitted ties or drawstrings. This way, the whole garment could be unraveled and reknitted into a new garment, which for me is how I feel the fashion industry should operate going forward. Designing garments with recycling in the initial design stages is crucial in order to reduce fashion waste in landfill.”
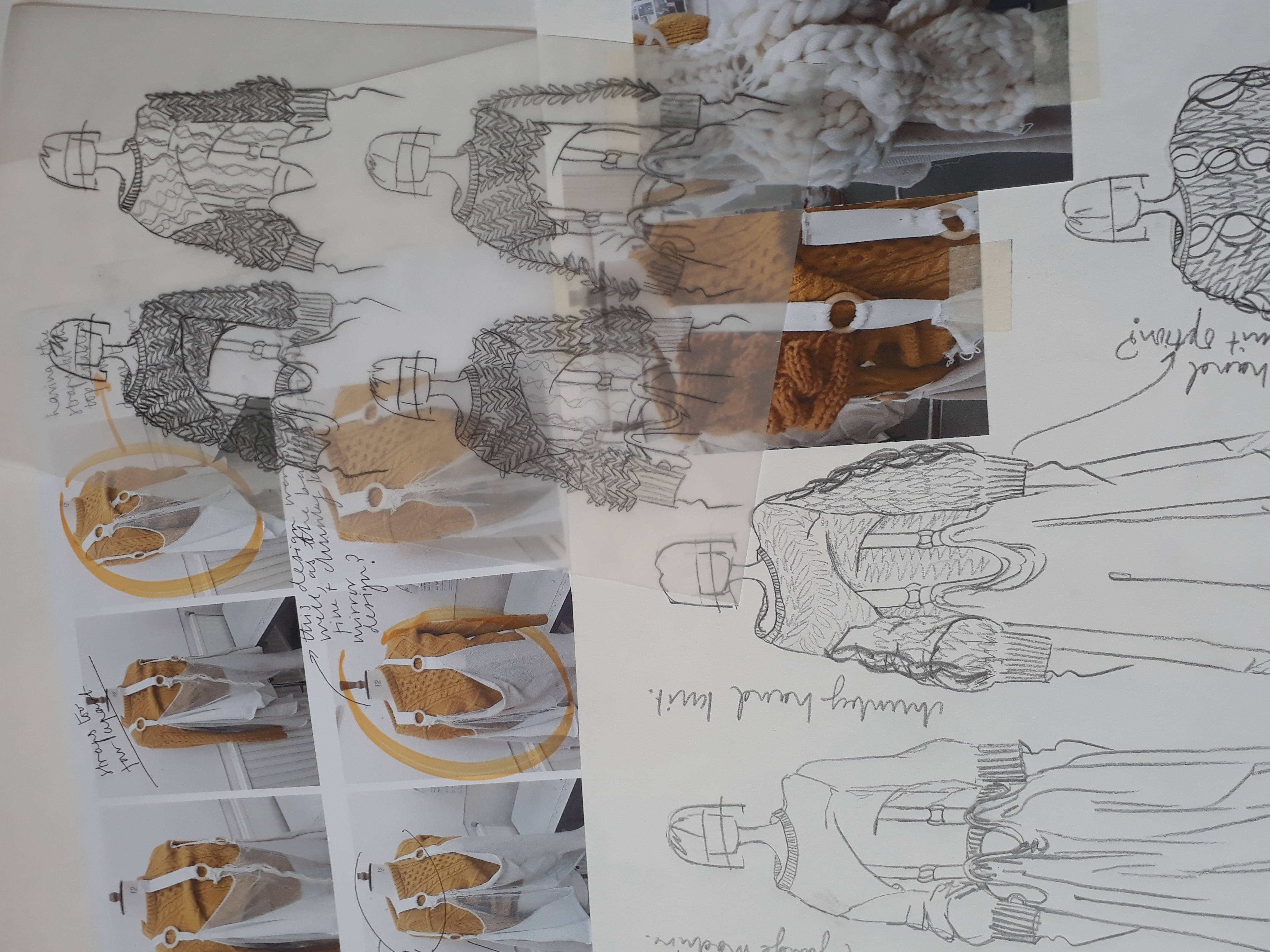
Inspired by vintage clothing and traditional craft techniques, Hannah’s visual research for her collection focused on Victorian Fisherman’s Ganseys from the North of England. The folklore behind the jumpers captured Hannah’s imagination, and the sense of identity within these character-encapsulating jumpers enriched her research.
Being relatively new to knitting, Hannah’s practical learning of stitch structures also inspired her design aesthetic as she learned each technique, by putting her own twist on her approaches to them.
The colour palette for Hannah’s award winning collection was curated through inspiration from the faded hues of ropes and fishing nets submerged in the ocean and resurfaced, with muted pastel shades, flecked with the original vibrancy of their florescence.
Aspiring to have an entirely British yarn palette, to support local businesses and reduce the Carbon Footprint of the collection, Hannah worked with Uppingham Yarns and Airedale Yarns to achieve as much transparency in her supply chain as possible. Also championing British Wool she used this in her collection to show the potential of the often-underrated fibre. Explaining this decision, Hannah said, “Much knitwear focuses on Merino Wool, which is a shame when British wool can be just as soft and luxurious when handled properly. So I decided to showcase the potential of British Wool in my garments.”
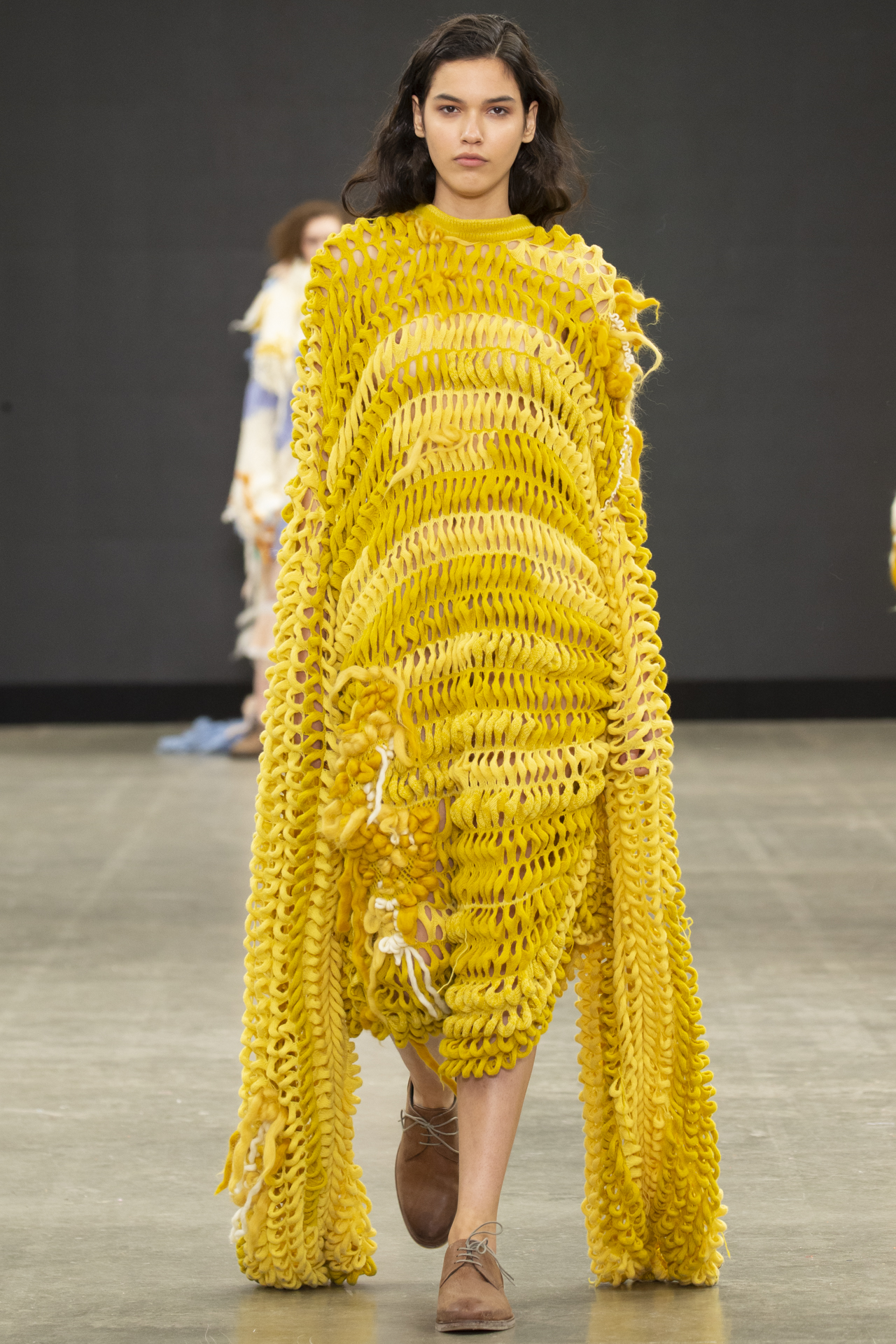
The hours of craftsmanship contained within each of Hannah’s GFW looks are a testament to her meticulous process. With great fondness for the crafting stages, Hannah recalled, “The quickest piece in my collection took only 36 hours, as it was a brushed stockinette stitch. The yellow loop dress was also a huge time investment. Once I’d cast on and knitted the trim, I’d put the 8 needles in action, knit 30 rows then move onto the next 8, repeating this across the whole bed. With a bed of 200 needles, it took 20 minutes to knit one row.”
Hannah’s favourite look in the collection was her knitted coat. By far the garment that took the longest to make, it involved over 120 hours at the knitting machine, including post machine weaving processes. Describing her painstaking attention to detail, Hannah went on, “I envisioned the coat as the showpiece of the collection so I wanted to incorporate all the different stitches I’d used so far – cables, plaits, lace holes, partial knitting. Each cable or plait was a different size and length so I made a spreadsheet to plan which cables required crossing on each row!”
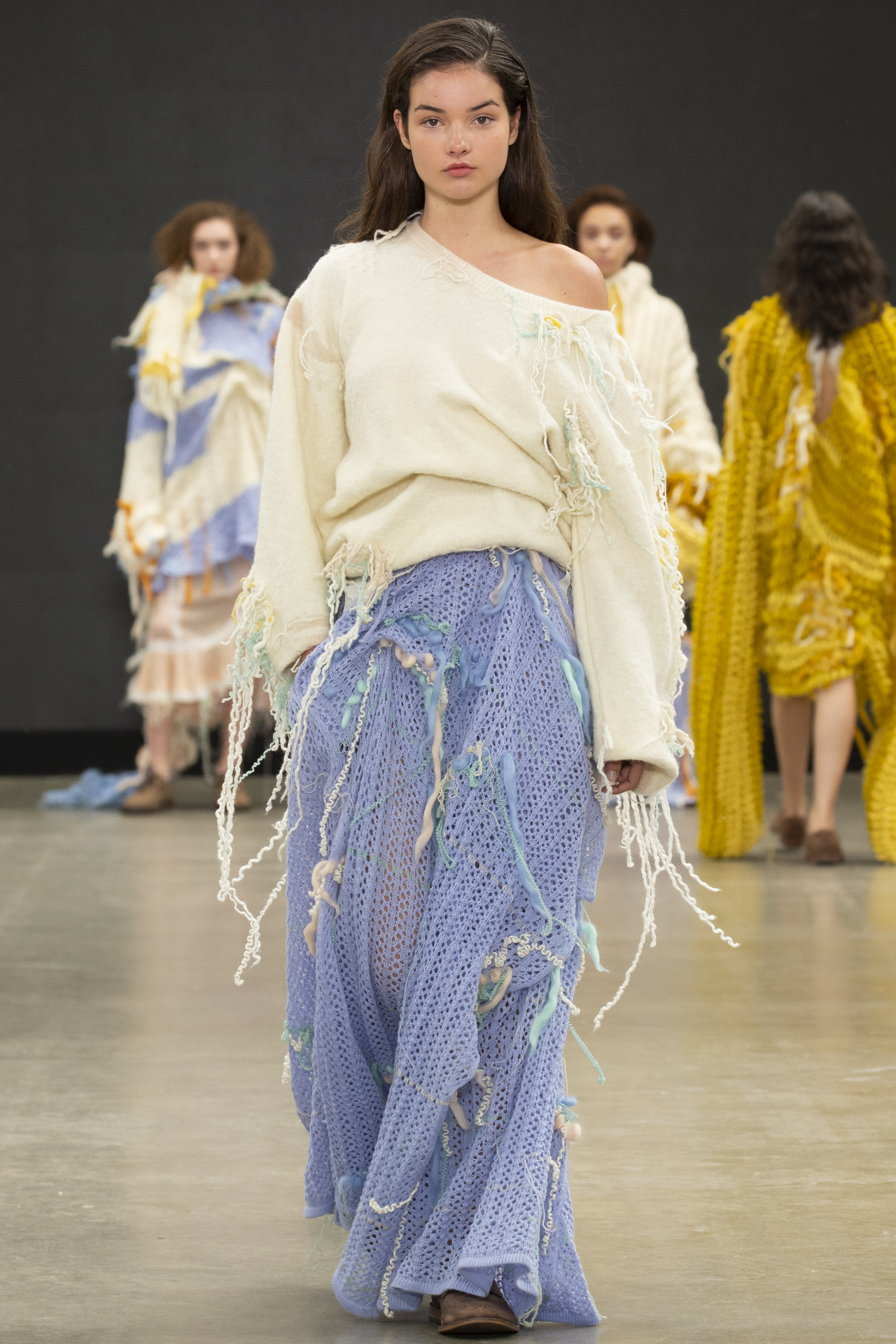
Hannah’s whole collection was knitted on a standard domestic machine. Sourcing parts of the now out of production machines is all part of the narrative for Hannah; it is the versatility of the humble domestic machine that she loves. The ability of the machines to handle such a vast variety of yarn weights and twists, combined with the power of the knitter to knit with the carriage whilst also hand manipulating stitches between rows provides endless opportunities for creative input. Domestics allow opportunity to challenge the traditional rigidity of the knitted row.
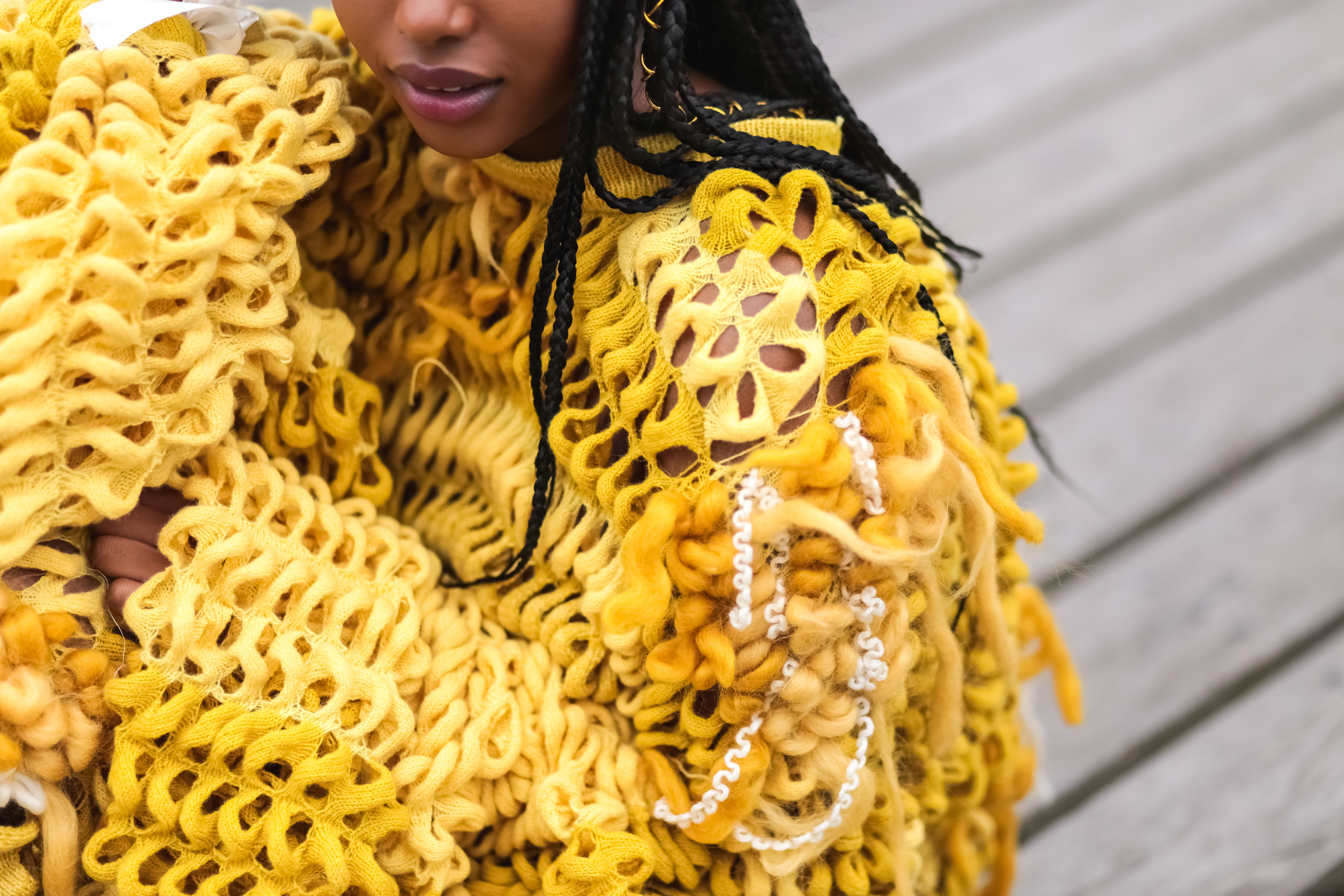
Winning the Catwalk Knitwear Award at GFW was something Hannah never expected, and was totally thrilled to receive. It boosted her confidence and gave credit to her vast and varied machine abilities, as well as her approach to fashion design. New to London, the chance to show her collection alongside such strong graduates was something Hannah described as a great privilege, and a wonderful way to end her university experience before entering the industry.
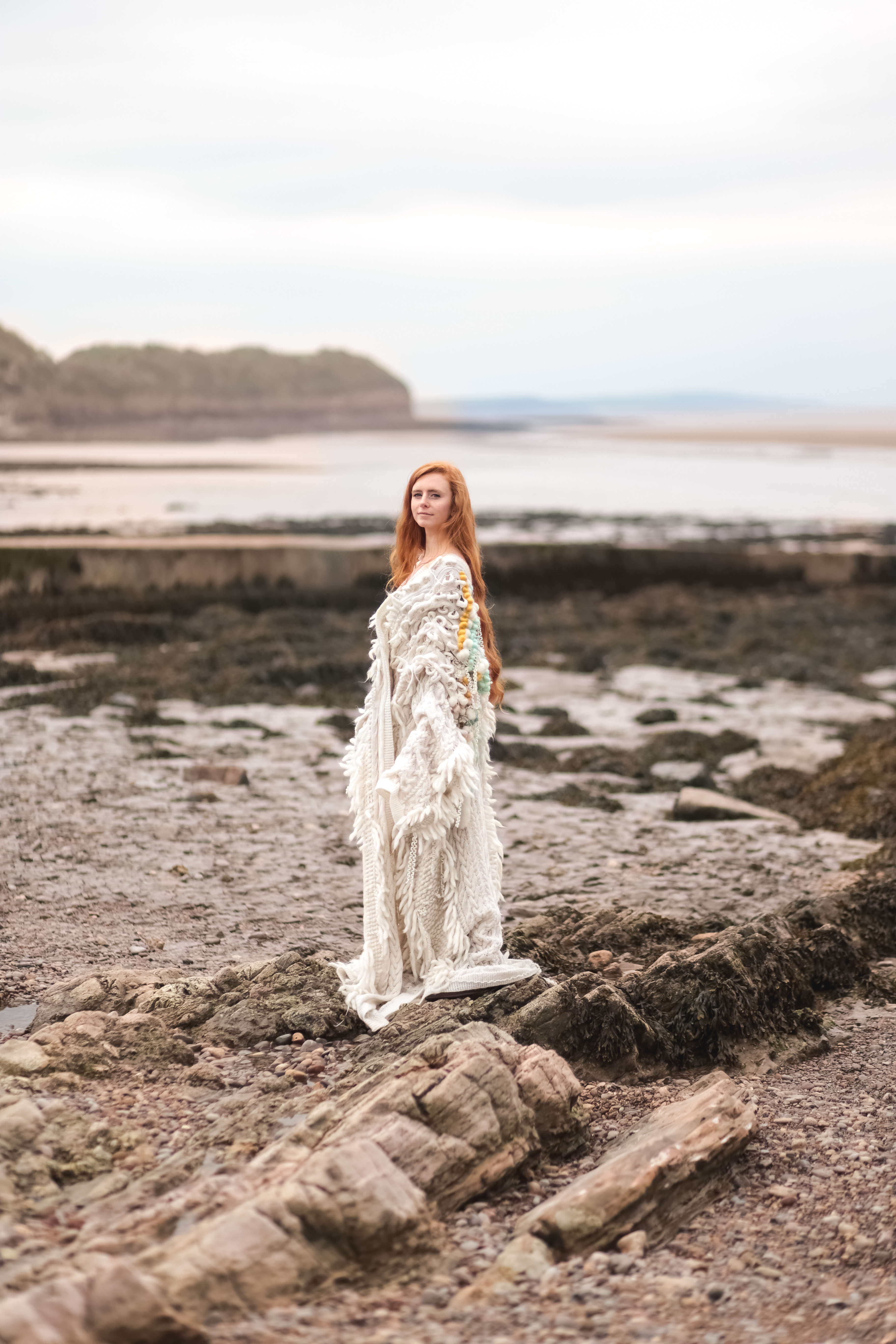
Having included so many techniques within her GFW collection, it’s hard to imagine what Hannah has left to explore for her future projects! Having only touched on the potential of partial knitting a little so far, Hannah plans to further explore the potential of this technique and others in future: “I loved working with partial knitting as you can make such dynamic and three-dimensional fabrics, which move so well when made into garments. I’ve also started experimenting more with intarsia and colour work. It’s another technique that can take a while, but can also create some amazing organic shapes. It’s also a successful way to mix lots of different weights of yarn without warping the knit, as more structured yarns can support thinner ones. I love texture in my knits, so any technique like weaving or e wrapping is also likely to appear in my work!”
Currently working on collaborations and commissions, Hannah is hoping to continue working freelance, and eventually have her own studio. Ultimately, the plan is to study an MA. Whatever path Hannah’s career follows, it is inspiring to have witnessed such a master class in taking the traditions of the domestic knitting machine and presenting a modern, award winning collection of knitwear. With only a year of knitting experience under her belt, it will be fascinating to see how Hannah’s garments evolve as she continues to learn even more, pushing the boundaries of what the often under valued domestic knitting machine can achieve.
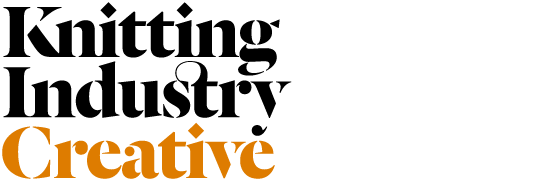
Subscribe To Our Newsletter
Join our mailing list to receive the latest news and updates from our team.